British Corner Shop opens Dutch distribution centre
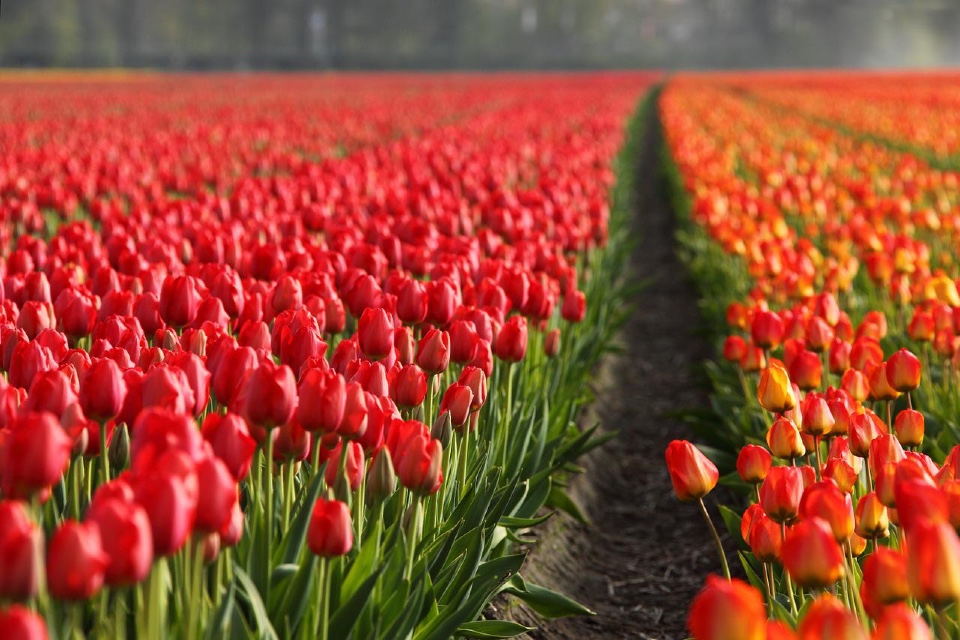
Online grocery store British Corner Shop has opened a new warehouse in Wijchen, The Netherlands – the first of its kind for the Bristol-based business as it seeks to offset the impact of Brexit and associated supply chain issues. The new distribution centre doubles the size of the company’s previous warehouse, allowing them to stock more of their extensive […]
PALLITE adds SLOTS to PIX range
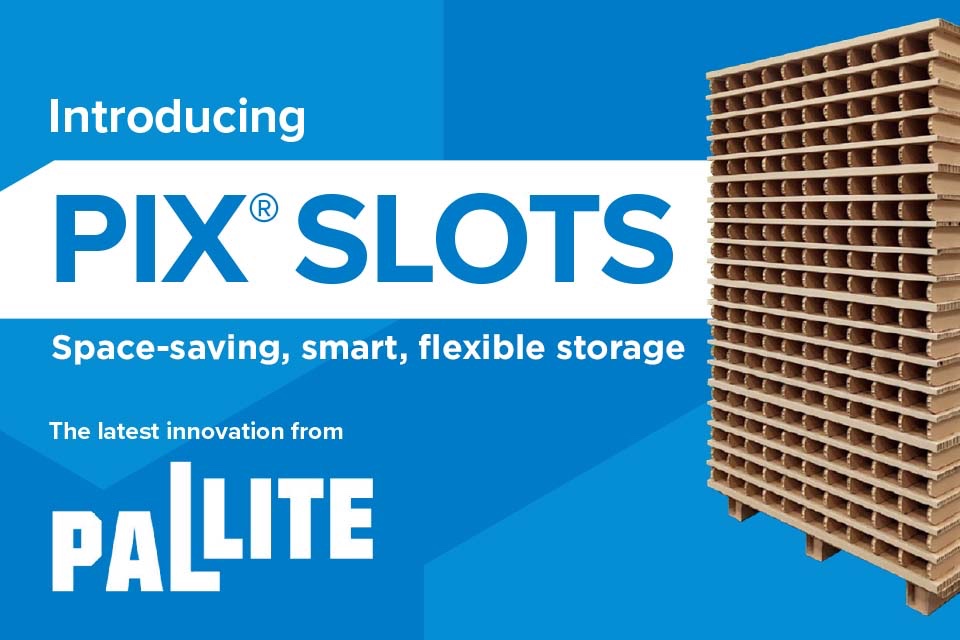
PALLITE®, designer and manufacturer of the popular PIX® range of flexible warehouse storage solutions, is expanding the brand range to include PIX® SLOTS, to meet the demands of businesses storing small and lightweight products, such as the fashion and beauty industry. PALLITE® launched its PIX® range over two years ago and has since taken the […]
Warehouse labour shortages – are robots the answer?
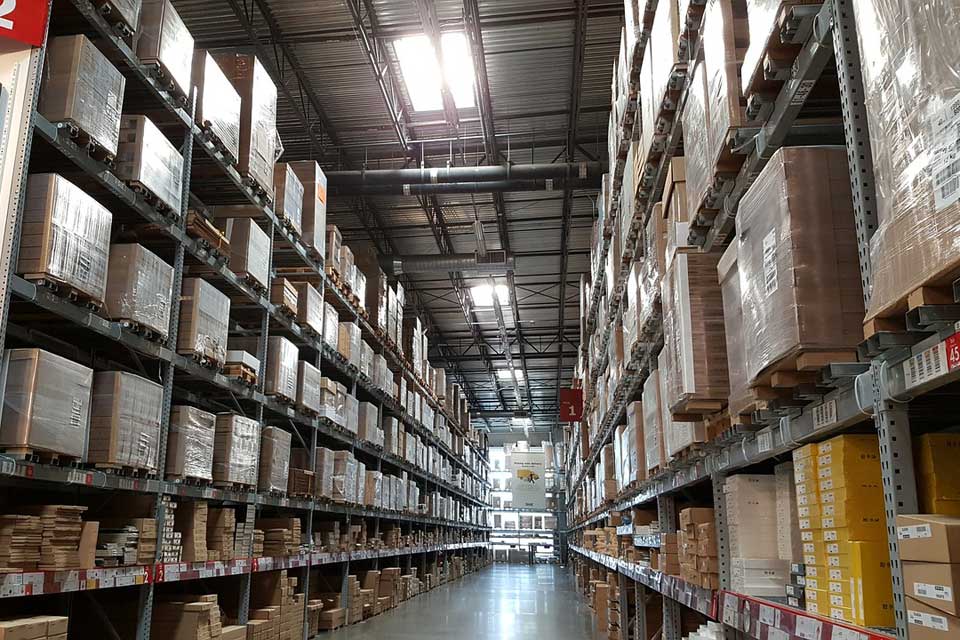
Collaborative robots could help tackle a looming labour shortage in UK warehouses by addressing the barriers deterring people from working in the sector, according to a new survey by fulfilment specialist 6 River Systems. The labour shortage is already impacting the hospitality and logistics sectors due to EU nationals returning to their home countries as a […]
UniCarriers: Your business, from every angle

By UniCarriers UniCarriers are a global supplier of forklift trucks and have over 50 years’ experience of supplying trucks and storage solutions to the UK market. Totally committed to developing the most efficient and cost-efficient materials handling and storage solutions, by providing a complete solution for your business, covering service, fleet information, health & safety, […]
Oxfordshire sees record take-up of industrial space in 2020
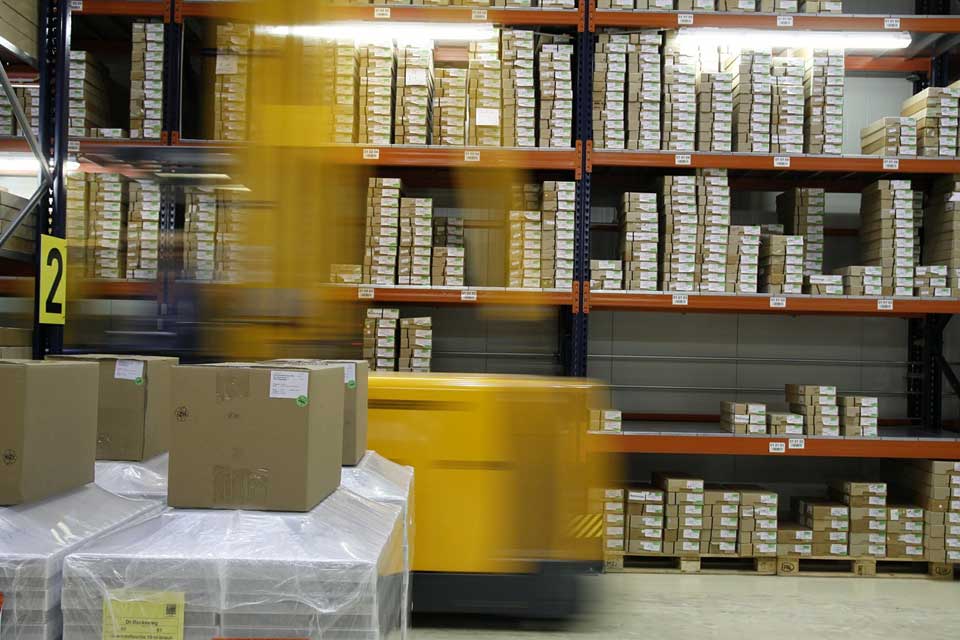
According to Savills, take up of industrial space in Oxfordshire hit 1.6 million sq ft (148,644 sq m) in 2020, a record year for the region and a 113% increase on the long term average. This can be attributed to a significant increase in demand, particularly from online retailers who accounted for 70% of all […]
New low lifting pallet trucks by UniCarriers: Safe and comfortable loading and unloading

UniCarriers introduces three new low lifting pallet truck models with a special focus on ergonomics and a multitude of customisation options. The global manufacturer of industrial trucks now offers the PLF, PLR and PLS models in three distinct lengths and with two different load capacities. The trucks were designed to assist loading and unloading, cross-docking, […]
The steps to deliver warehouse automation
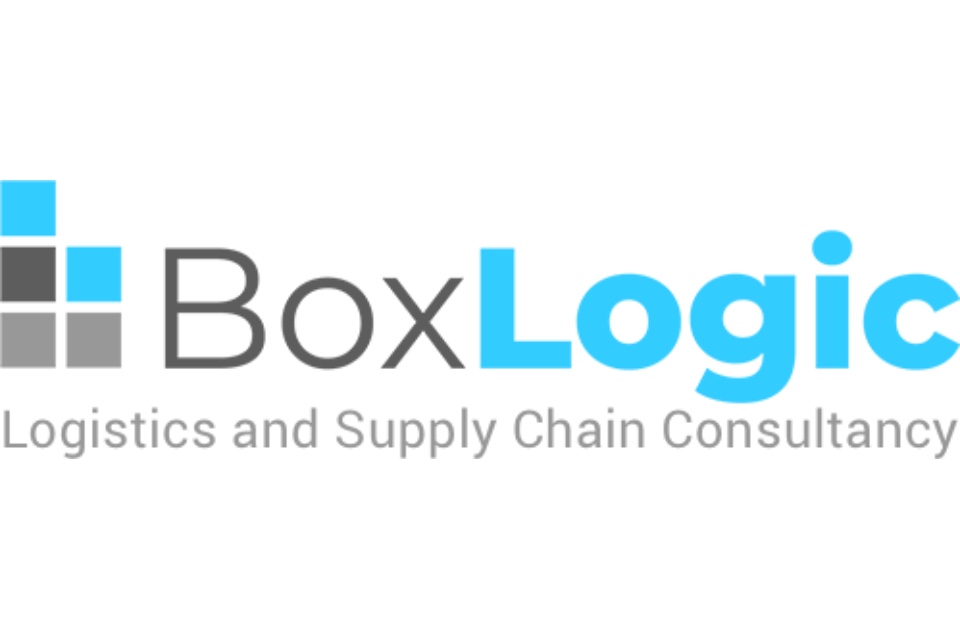
By BoxLogic BoxLogic offer expert logistics consultancy support for businesses looking to transform their operations and reduce costs, increase capacity, or improve service. Warehouse automation is one area of specialisation for our consultants where we use our extensive experience to support our clients develop a costed concept design through to tendering and implementation. While the […]
The Hut Group readies £31m Manchester logistics site
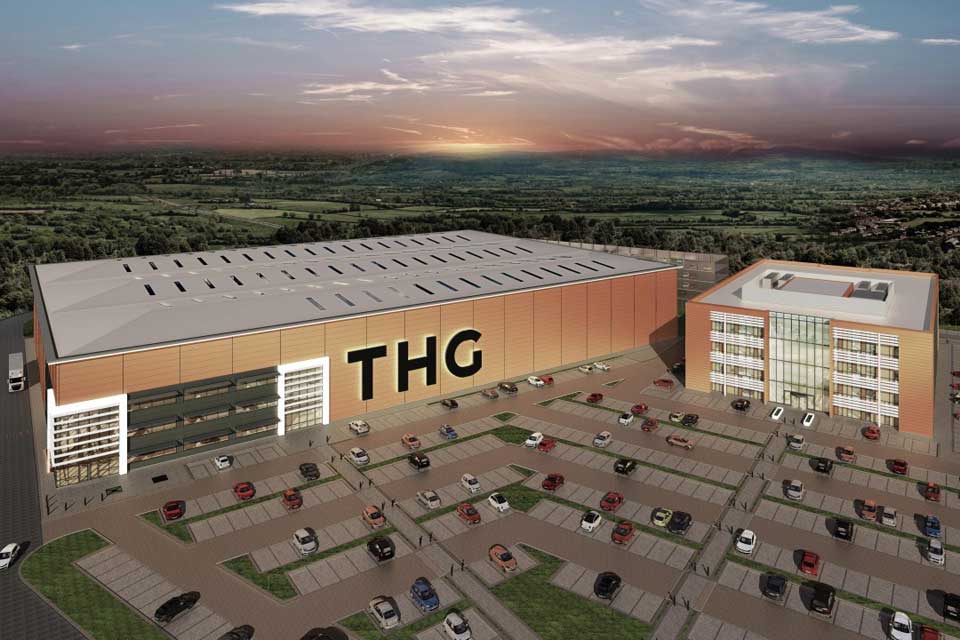
A new £31m development housing The Hut Group’s new 168,000 sq ft warehouse and 104,000 sq ft office space next to Manchester Airport has been approved. The project will be delivered by Icon Industrial at its 45-acre warehouse and logistics site at the airport, including a new 280,000 sq ft office building at Airport City […]
Nestlé and XPO Logistics building ‘digital warehouse of the future’
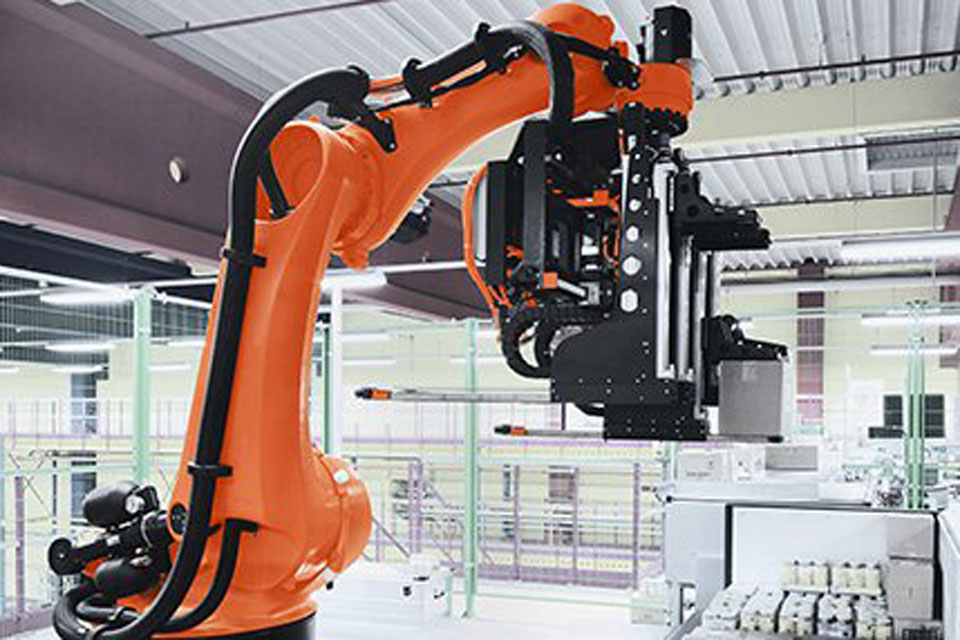
Nestlé and XPO Logistics are co-creating a 638,000-square-foot distribution centre at the new SEGRO East Midlands Gateway Logistics Park in Leicestershire. The facility, described as a ‘digital warehouse of the future’, will be occupied predominantly by Nestlé for its consumer packaged goods and will function as a testbed environment for XPO technology prototypes prior to […]
Davies Turner opens multi-user distribution centre in Bristol
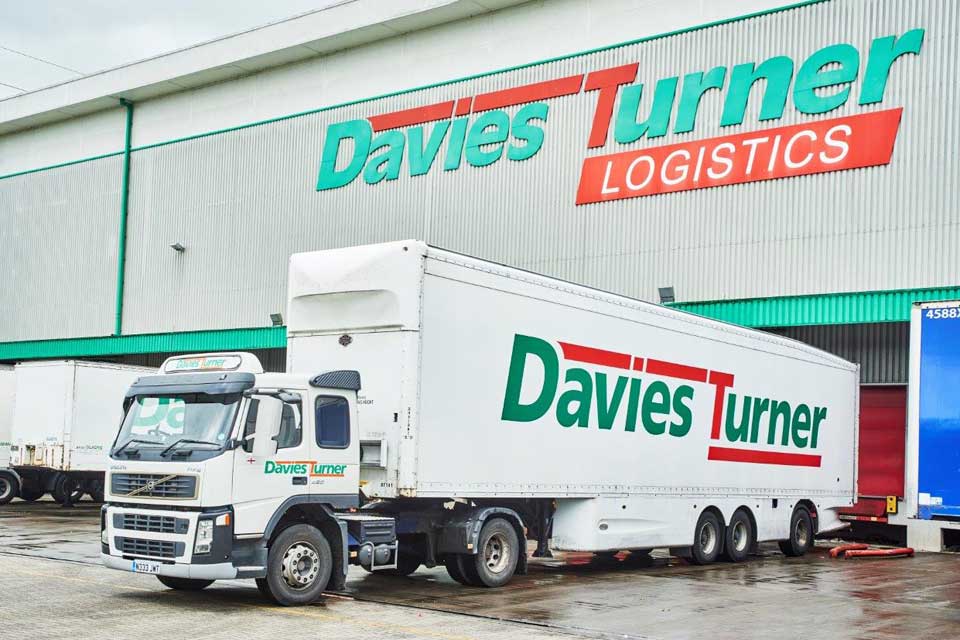
Davies Turner says its new multi-user distribution centre near Avonmouth, Bristol, is now fully operational. The new hub at Central Park by Western Approach is the company’s largest to date at 150,000 sq ft (14,000 sq m) and adds to its nationwide warehousing network. The building has a high bay fully racked area, with a […]