INDUSTRY SPOTLIGHT: Aramex shipping & logistics
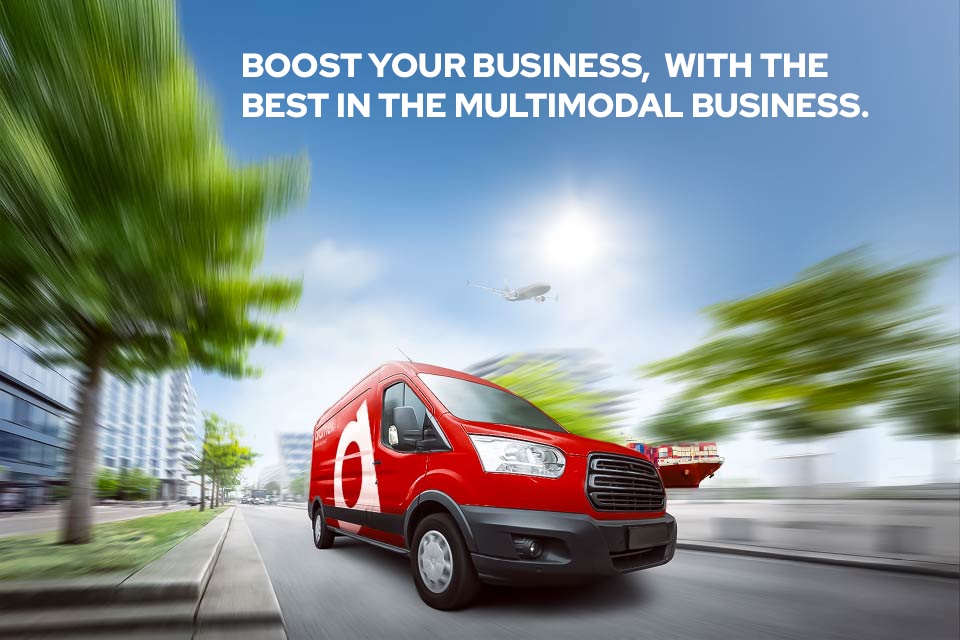
As a global logistics provider and partner with a 40-year track record in over 70 countries, Aramex is always within reach. We offer seamless, cost-effective air, sea, road, and rail, multimodal solutions for UK businesses. International Express Aramex’s International Express service ensures your shipments reach global destinations quickly and efficiently, with real-time tracking and door-to-door service for ultimate […]
How are shippers and carriers implementing AI?
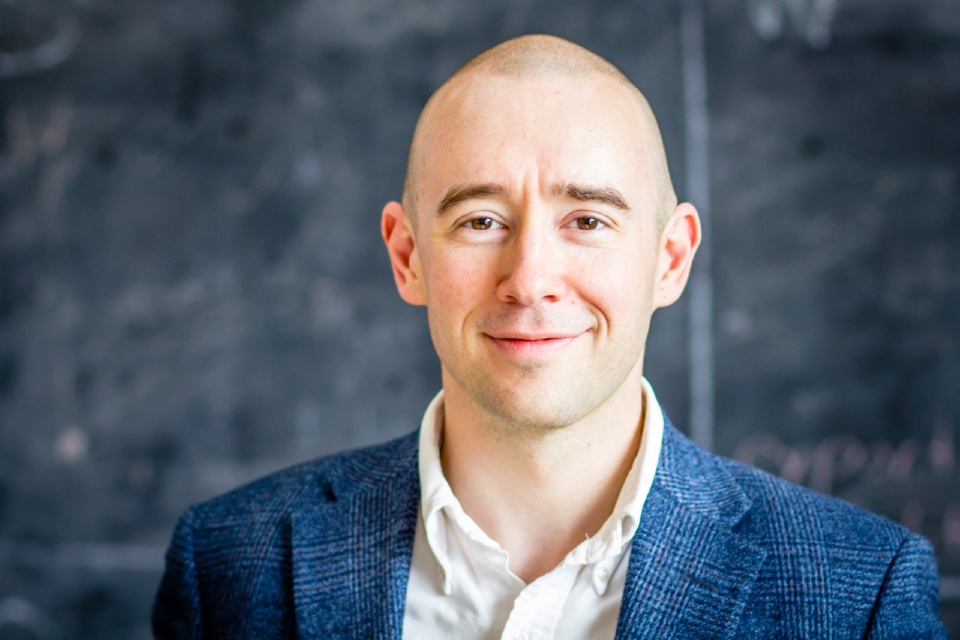
By Jonah McIntire, Chief Platform Officer at Transporeon, A Trimble Company Shippers, carriers and logistics service providers (LSPs) alike have been slowly adopting AI for almost a decade. So, in a sense, AI is nothing new. What is new, however, is the meteoric rise of generative AI. The buzz around this reached a fever pitch […]
OPINION: Red Sea Crisis underlines the need for greater data transparency
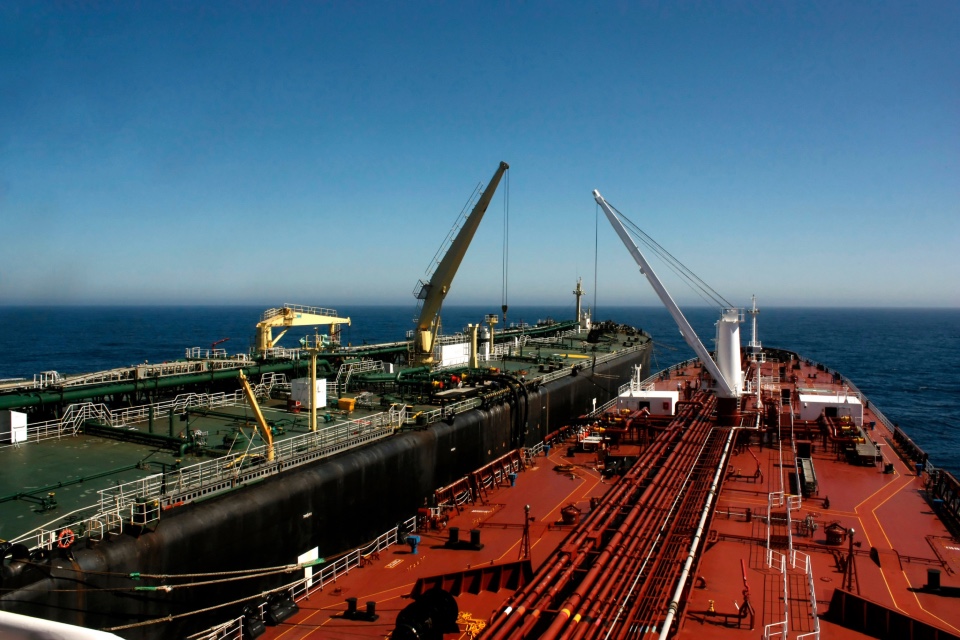
The speed with which shipping companies have responded to the crisis in the Red Sea underlines the growth of digitisation and utilisation of diverse data resources to support complex decision making. But data issues, from ownership to a lack of open integration, remain a challenge explains Captain Steve Bomgardner, Vice President – Shipping & Offshore, […]
Red Sea impact on UK retailers – Who foots the bill?
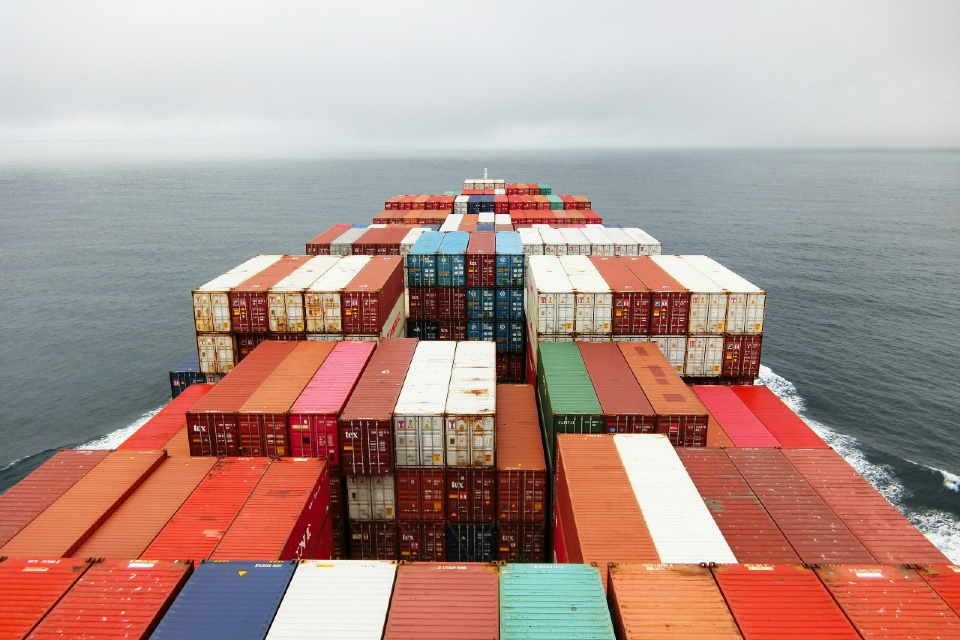
Ongoing attacks by Houthi rebels on cargo ships in the Red Sea are continuing to cause supply disruptions for retailers, as stock deliveries have been delayed and many vessels have been forced to reroute around South Africa’s Cape of Good Hope. The route can add an extra 10 to 14 days to cargo ships’ journey […]
Combatting a new era of maritime sanctions evasion
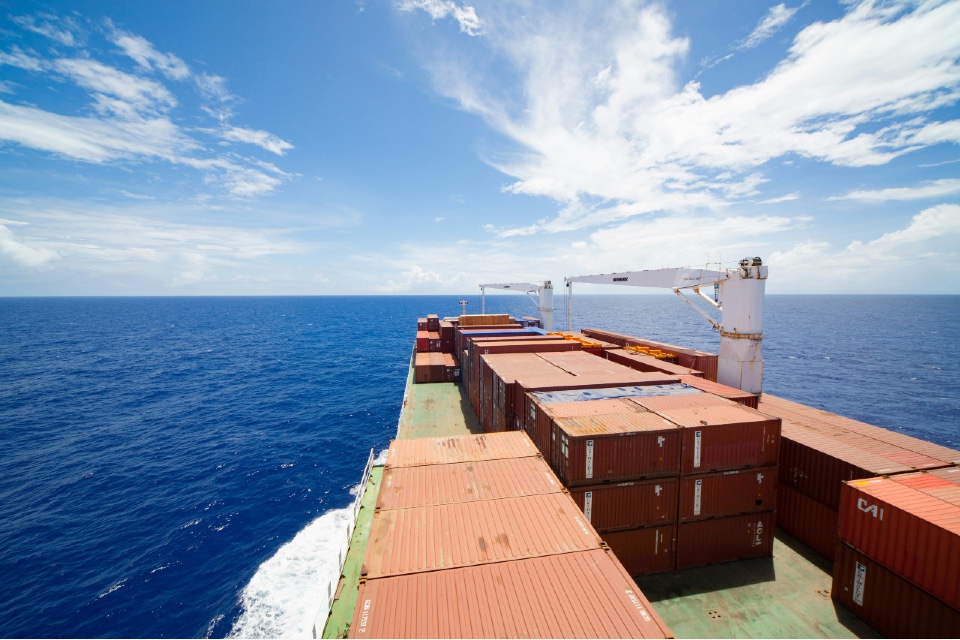
Recent years have seen a notable increase in deceptive shipping practices (DSPs), particularly in the form of AIS spoofing and dark fleet activity. The implementation of Russia-related sanctions and a price cap on the sale of Russian oil and petroleum products has led threat actors to turn towards more sophisticated forms of sanctions evasion. Their […]
Building the business case for Satellite IoT
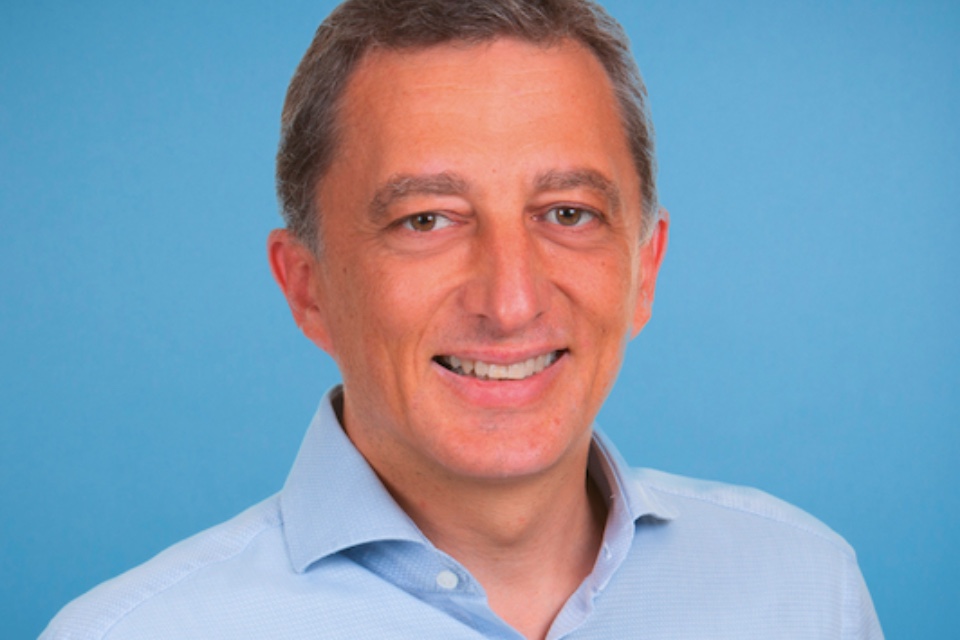
The Operational IoT market continues to expand as organisations across the world imagine an extraordinary range of opportunities to leverage sensor technology. Weather monitoring stations are transforming the efficiency and environmental performance of remote copper mines and helping farmers to safeguard crops and livestock in a changing climate. The shipping industry is improving cargo traceability […]
DOWNLOAD: Shipping and Distribution – The State of the Deskless Workforce
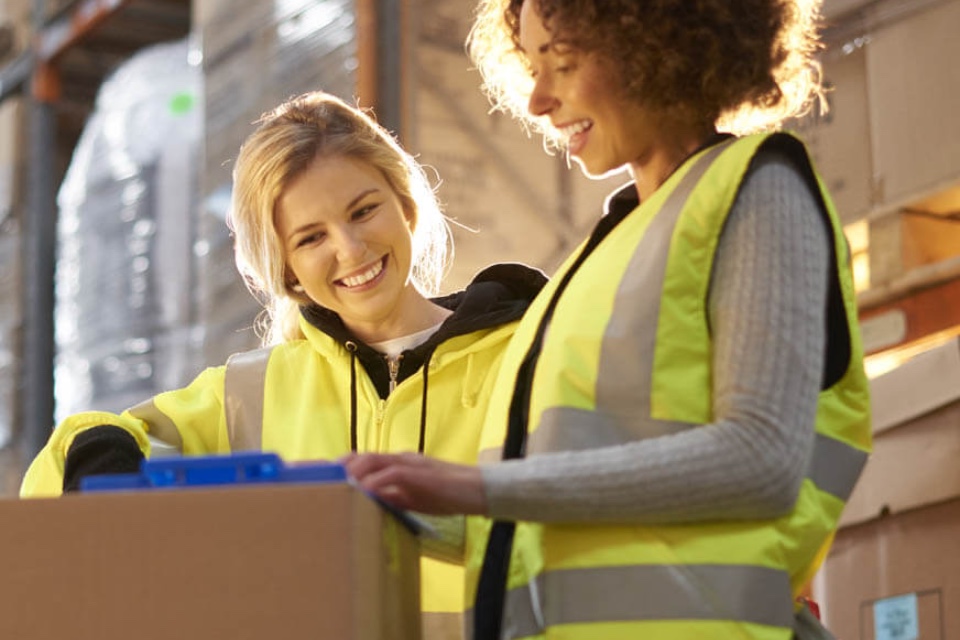
Are staffing problems leaving your business high and dry? Download Quinyx’s new report for invaluable employee retention and scheduling advice. Current worker shortages in the UK are continuing to cause problems. Many firms are desperately trying to avoid business disruption as they attempt to plug staffing gaps, whilst running the risk of overworking existing team members […]
WEBINAR: Managing cost volatility with forecasting – a practical roadmap with SLG Brands

By Zencargo With global shipping costs inflated to unprecedented highs, getting a total view of the costs of your supply chain has never been more important for a business. In fact, in a recent roundtable of 25 supply chain leaders[1], 56% said that ‘improving overall data quality for more informed decisions’ was the one approach that […]
ABP invests in Port of Lowestoft to support UK Southern North Sea energy sector
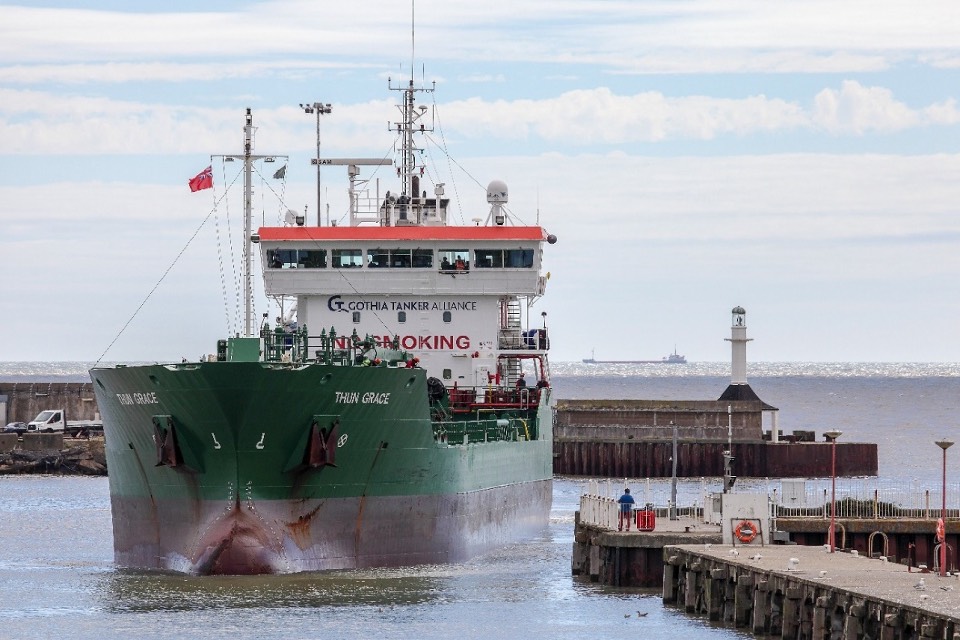
Associated British Ports (ABP), the owner and operator of the Port of Lowestoft has invested more than £250,000 in the construction of a new fuel bunkering facility to support the UK Southern North Sea (SNS) energy sector. Yesterday, the bunkering facility received its first fuel from the vessel, Thun Grace, which called at the Port […]
New container shipping association established

A.P. Moller – Maersk, CMA CGM, Hapag-Lloyd, MSC and Ocean Network Express plan to establish a new container shipping association. The move is intended to ‘pave the way for digitalisation, standardisation and interoperability in the container shipping industry’. In addition, IT executives from A.P. Moller – Maersk, CMA CGM, Hapag-Lloyd, MSC and Ocean Network Express […]