A secure, sustainable pathway to the IoT in supply chains

By Derek Bryan, VP EMEA at Verizon Connect Supply chains are constantly battling challenges, with unforeseen delays, restrictions and thefts causing disruption at every turn. More recently, the pandemic threatened the continuity of supply chains more severely than any event in recent memory. Lockdowns imposed across Europe and the rest of the world in response have caused […]
Why digitising supply chains can help pay for itself
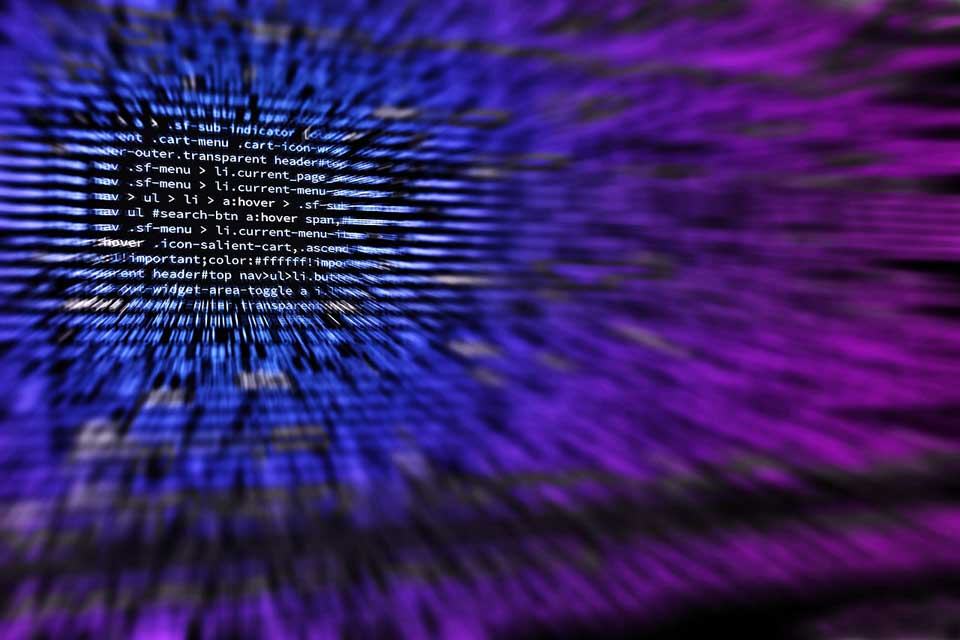
By Derek Bryan, VP EMEA, Verizon Connect For some businesses, digital transformation represents an opportunity to improve how it operates and connects with partners and customers; for others, it can seem like a headache with a considerable price tag attached. While it’s true that any change requires careful planning, those in the ‘loathe camp’ may […]
Quarter of commercial drivers ‘breaking rest rules’

Twenty-five per cent of commercial drivers in the UK are flouting rules around rest and fatigue, according to a survey of fleet managers from Verizon Connect. In terms of key concerns, 24 per cent of fleet managers cited compliance, 23 per cent said unsafe driving practices and 13 per cent of said drivers not taking rest. […]