How to build resilience into Supply Chain 4.0 strategies
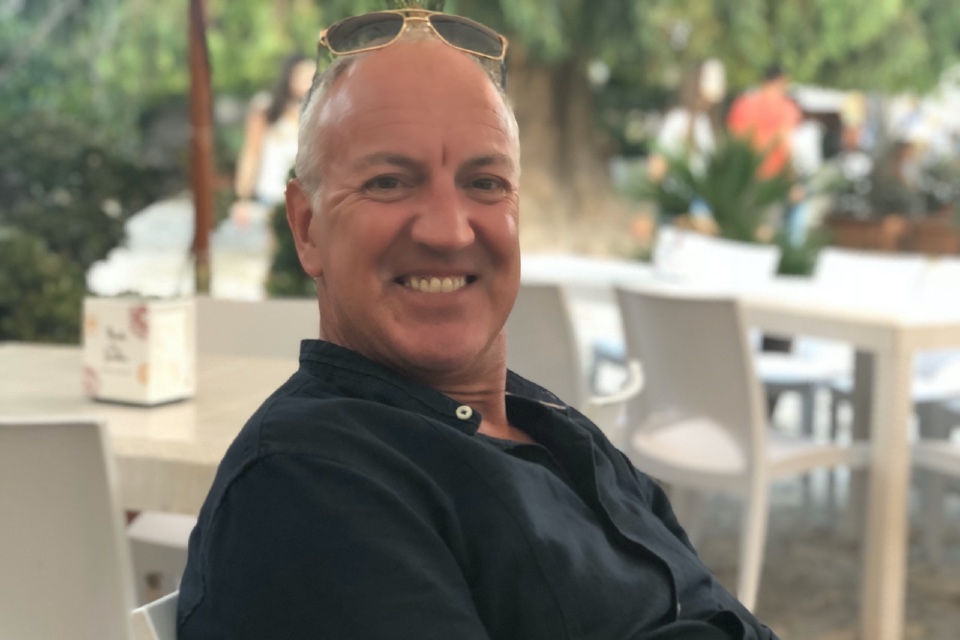
By Ian Terblanche (pictured), Strategic Sales & Channel Director at Sigfox With the rise in supply chain disruptions during COVID-19, companies may already have an eye on streamlining and improving supply chains but they are also under immense pressure to manage supply chain disruption. When examining the challenges faced by supply chains today, companies need […]
IoT accelerates end-to-end supply chain visibility
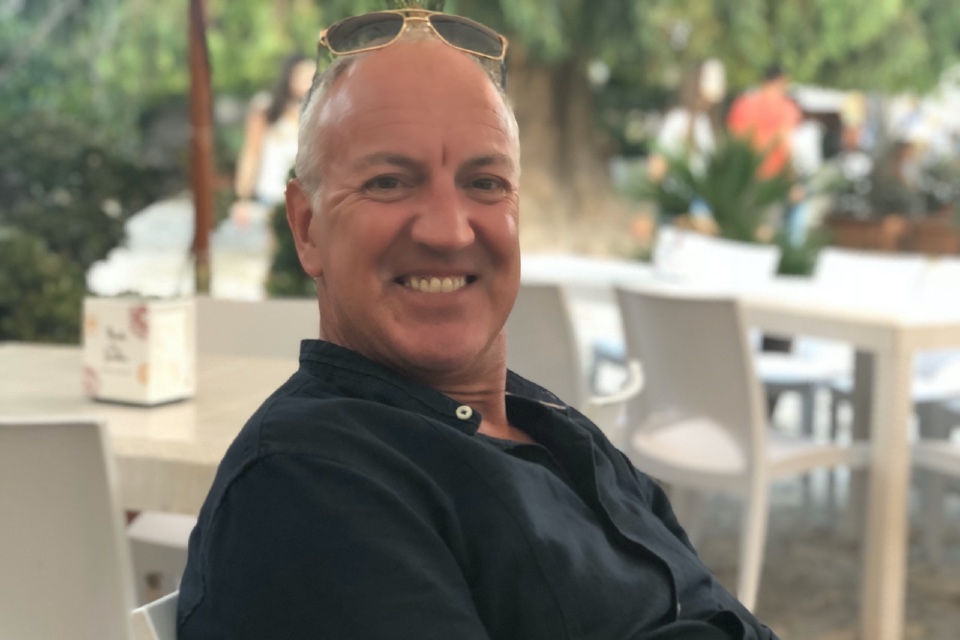
By Ian Terblanche, Global Sales Director at Sigfox The global supply chain and logistics market is set to exceed $15 trillion by 2024, developing at a CAGR of 6.0% from 2016 to 2024 by volume. However, in spite of these impressive growth figures, there has been a mere trickle of innovation in the supply chain market, […]