Is a UK-EU Veterinary Standards Agreement on the horizon? Implications and challenges
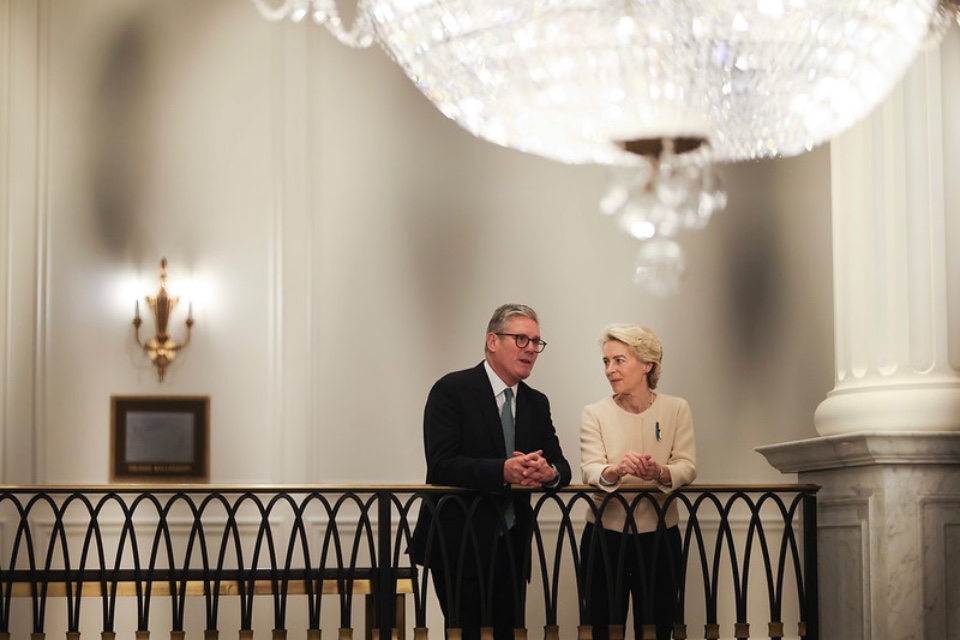
By Alinea Customs The United Kingdom’s departure from the European Union created regulatory challenges, particularly in veterinary standards. In 2020, whilst EU Commission Vice-President Maroš Šefčovič proposed an equivalence agreement on veterinary safety standards, it was rejected by the UK due to concerns over European Court of Justice (ECJ) jurisdiction. With the UK-EU Summit in […]
Building supply chain resilience in 2024
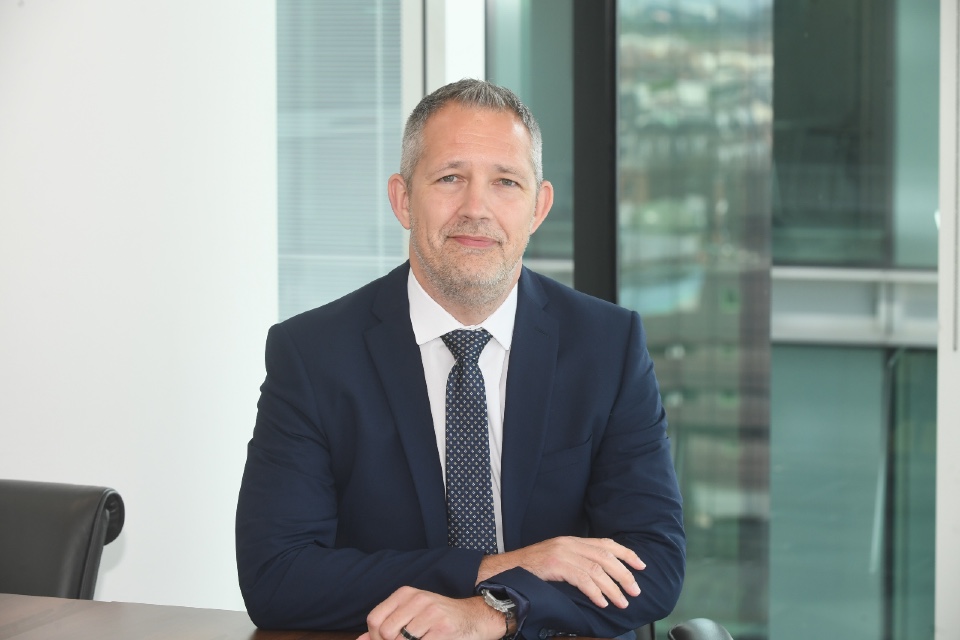
By Fraser Paget (pictured, above), BDO In 2024, UK businesses face a rapidly evolving landscape, with supply chain resilience becoming a critical priority. While businesses have mostly adapted to the disruptions caused by Brexit and COVID-19, new and equally complex challenges have emerged. Today’s businesses are navigating geopolitical tensions, inflation, sustainability demands, and technological shifts. […]
How can manufacturers mitigate the lasting effects of COVID-19 and Brexit?
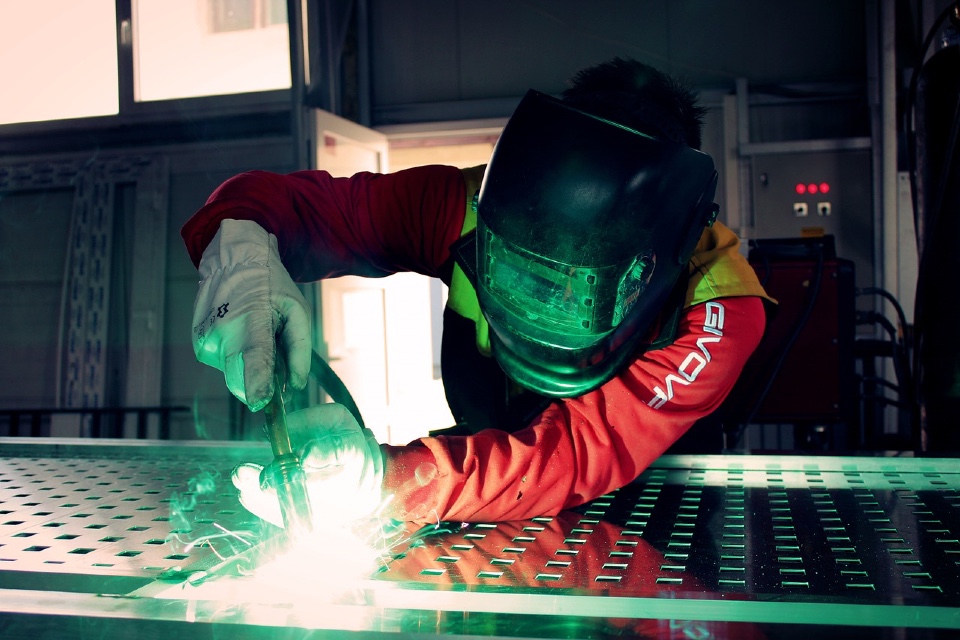
It’s no secret that COVID-19 and Brexit have had a lasting effect on a wealth of businesses. In particular, the manufacturing sector has been heavily impacted due to the UK’s withdrawal from the single market and the subsequent restrictions on imports and exports. However, many manufacturers are optimistic at least in the short term, and […]
CDS is here – And this time, it’s for real
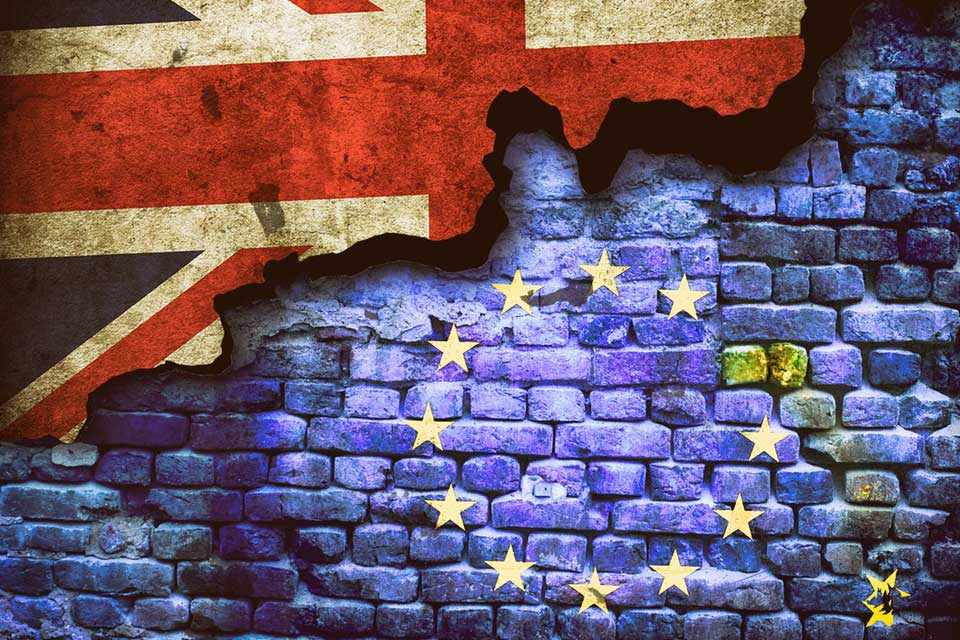
By Martin Meacock, Vice-President of Product Management, Descartes With a global pandemic, chaos at the borders, an HGV driver shortage and ensuing supply chain chaos, compounded by political uncertainty, inflation and a fuel and energy crisis – it’s fair to say UK business has had a challenging few years. And that’s not to mention Brexit. Since […]
Modi’s vision for India ‘makes economic powerhouse crucial partner’ for Britain
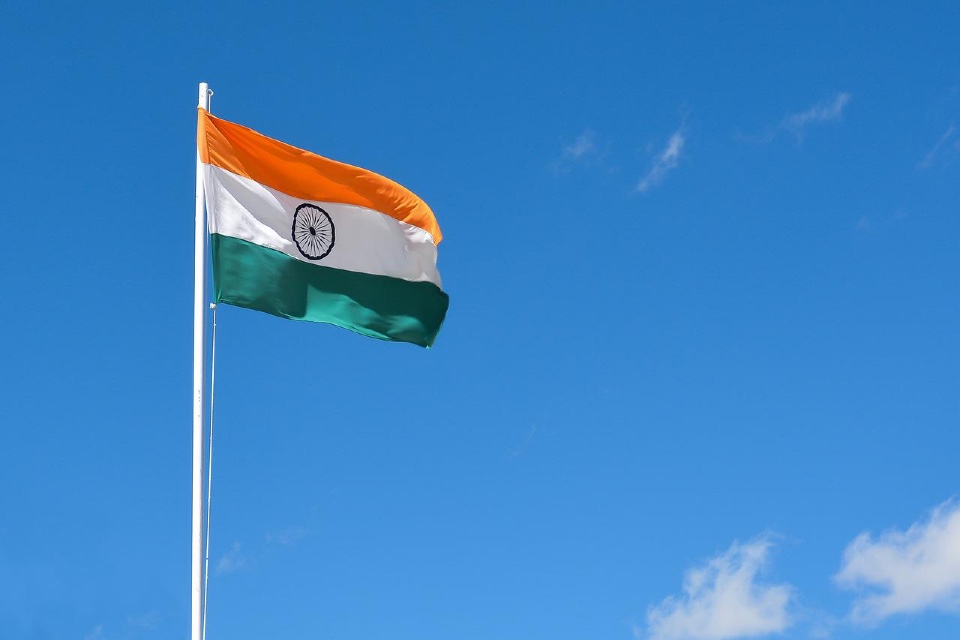
UK Trade Secretary, Anne-Marie Trevelyan, is meeting with India’s trade chief, Piyush Goyal, on Friday for the fourth round of talks on a trade deal between both countries. This is a matter of urgency for the government, as officials rush to get the agreement over the line by October 24. India is predicted to grow at the […]
British Corner Shop opens Dutch distribution centre
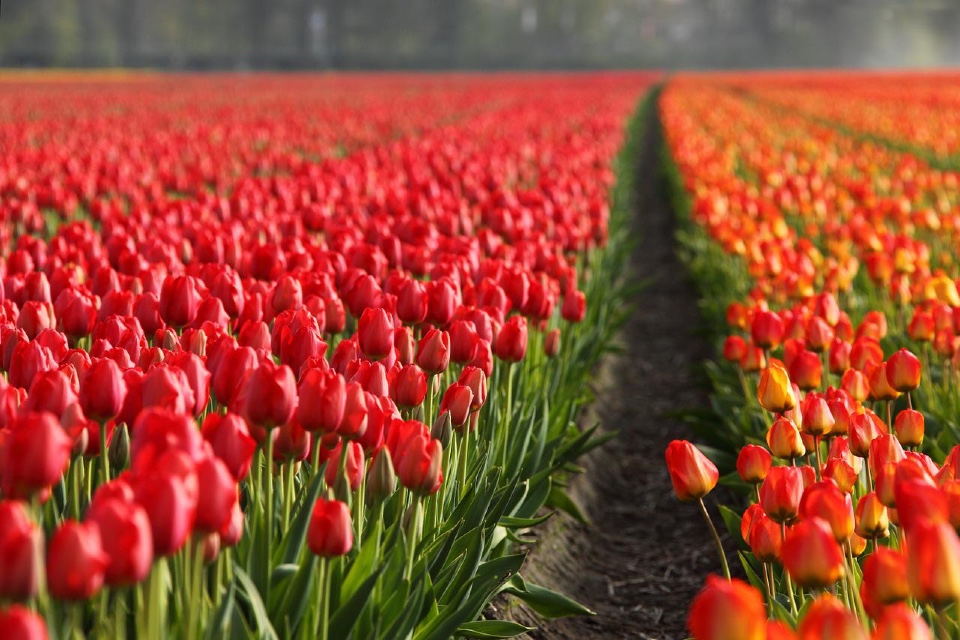
Online grocery store British Corner Shop has opened a new warehouse in Wijchen, The Netherlands – the first of its kind for the Bristol-based business as it seeks to offset the impact of Brexit and associated supply chain issues. The new distribution centre doubles the size of the company’s previous warehouse, allowing them to stock more of their extensive […]
World Supply Chain Day: Creativity in the electronics industry will counter chip shortages

Thanks to Brexit, the pandemic and now the Russia/Ukraine war, the risks and shortfalls in our global supply chains have become front and centre for most companies over the last two years, especially for the electronics industry. Supply chains are increasingly recognised as a key component to business survival, success and growth, as ByteSnap found […]
Five ways UK exporters are bucking the trend and thriving in Ireland
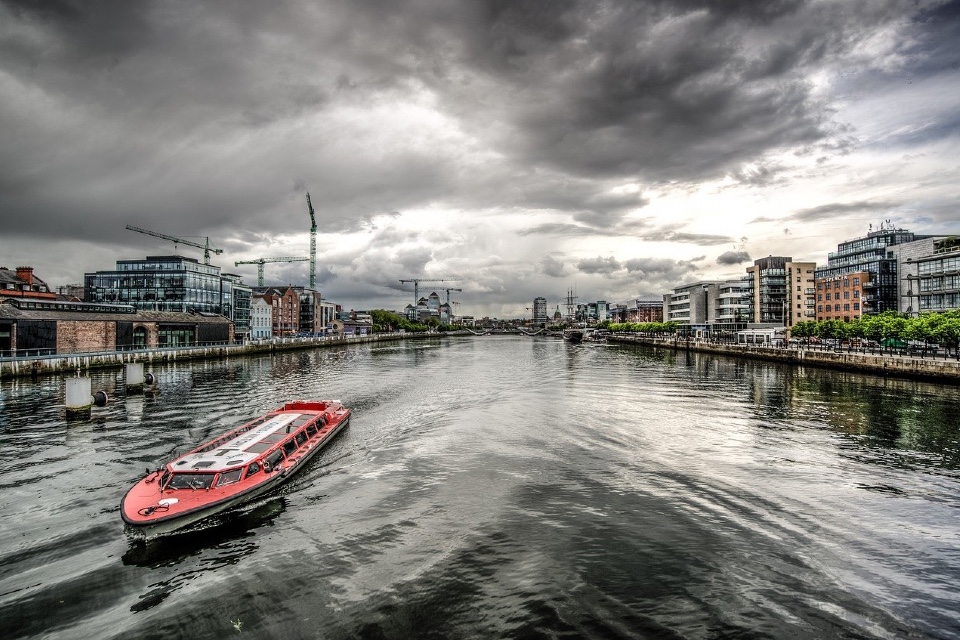
In a market boosted by young consumers with a willingness for cross-border spending online the Irish eCommerce market is predicted to grow to be worth a staggering €7bn in 2022. The latter half of 2021 saw Irish consumers turn in increasing numbers to buying from international retailers. Yet last year exports from the UK to […]
INDUSTRY SPOTLIGHT: T S Europe helps you manage logistics uncertainty

The lorry driver shortage is making headlines again. Grocery store shelves are empty, the prices of goods are increasing, and businesses are beginning to worry. The logistics world is volatile as industries are faced with the challenge of acclimating to the new, demanding changes. Amid the chaos, Transport Services Europe has embraced the storm and […]
EU VAT changes – is your eCommerce business ready?
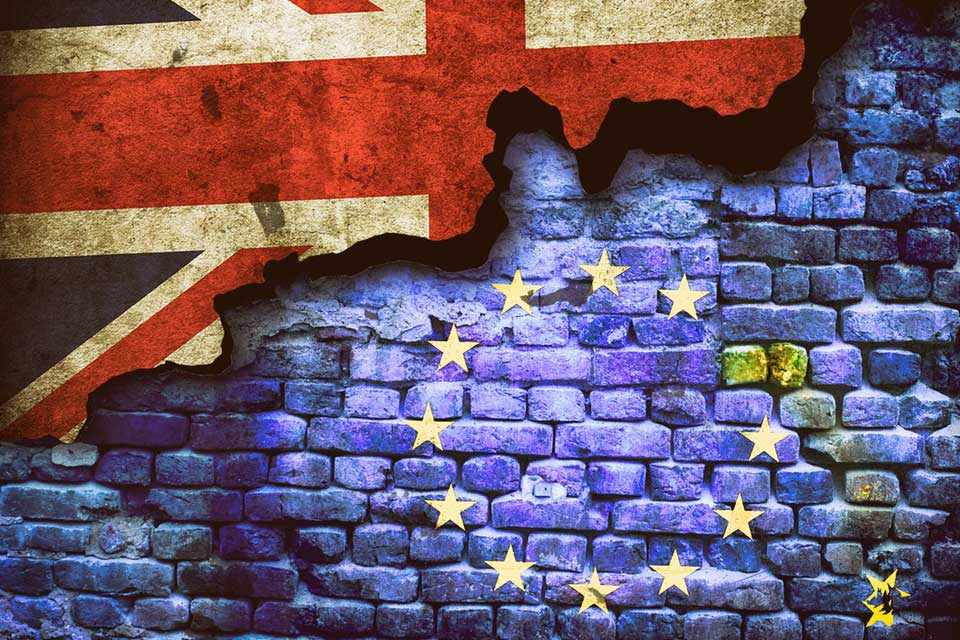
Doing business with Europe has become so expensive and onerous since Brexit that a vast number of UK eCommerce businesses have simply turned off all EU activities. Managing the different VAT thresholds and rates across each EU country has certainly added to the admin burden and cost of doing business – so how much difference will the […]