Discover the latest innovations in supply chain, distribution and logistics
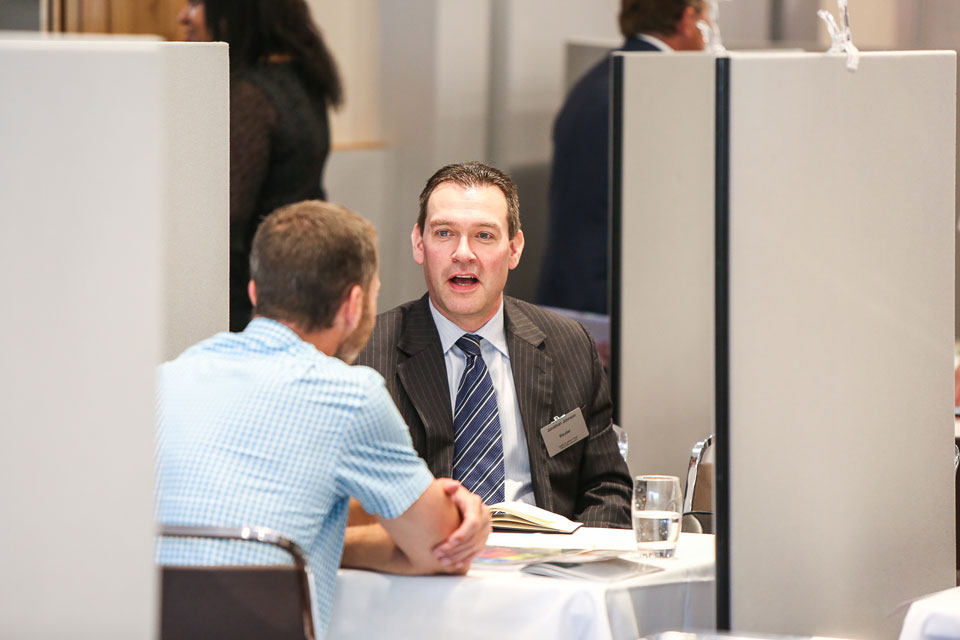
We’d like to invite you to the Total Supply Chain Summit on May 18th & 19th 2020 at Heythrop Park, Oxfordshire. Meet with new suppliers, attend insightful seminar sessions and network with fellow senior supply chain, distribution and logistics professionals. Plus, your complimentary guest pass includes overnight accommodation, all meals and refreshments and an invitation to our networking dinner […]
5 reasons you can’t miss the Fleet Summit
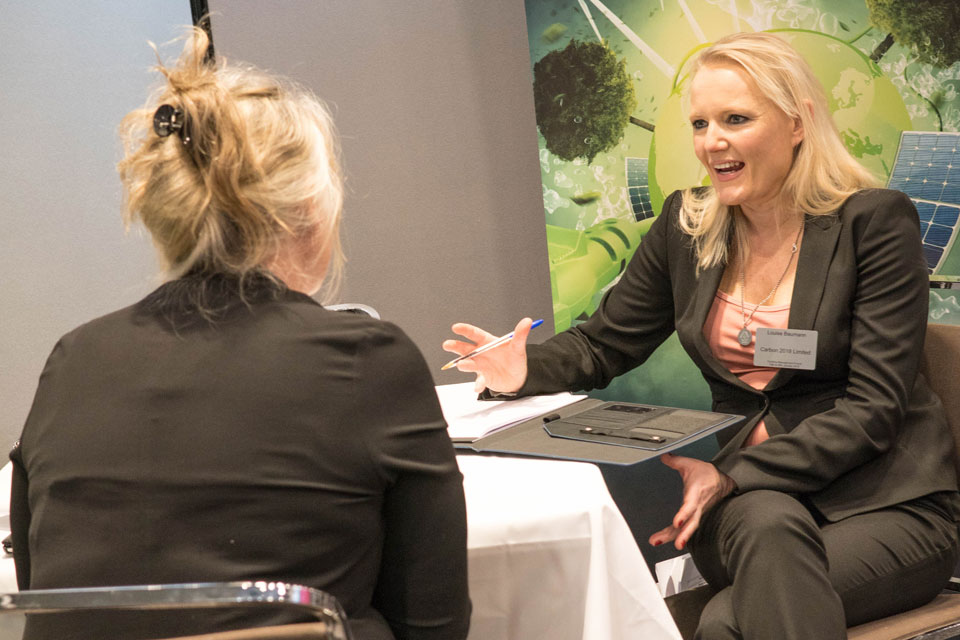
Register today for the Fleet Summit – It’s FREE for you to attend and could help reduce your expenditure by matching you up with innovative suppliers who match your business requirements. As one of our VIP guests, you’ll be joining just 60 other senior fleet managrment professionals who are attending the event to network, learn […]
Do you specialise in Distribution services? We want to hear from you!
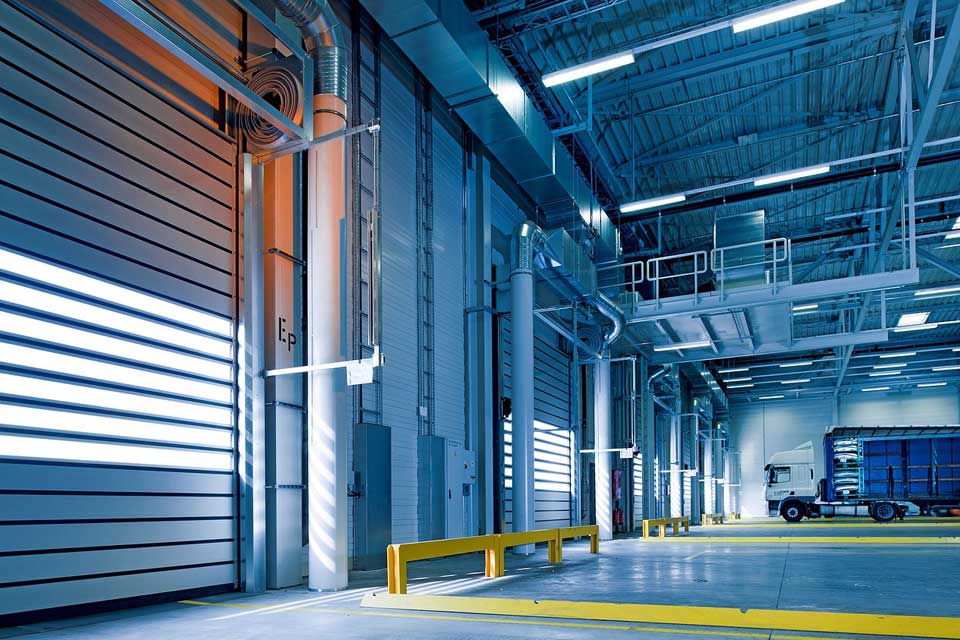
Each month on Supply Chain Briefing we’ll be shining the spotlight on a different part of the logistics market – and in February we’ll be focussing on Distribution. It’s all part of our ‘Recommended’ editorial feature, designed to help supply chain industry buyers find the best products and services available today. So, if you’re an Distribution specialist […]
Total Supply Chain Summit – Complimentary places going fast!
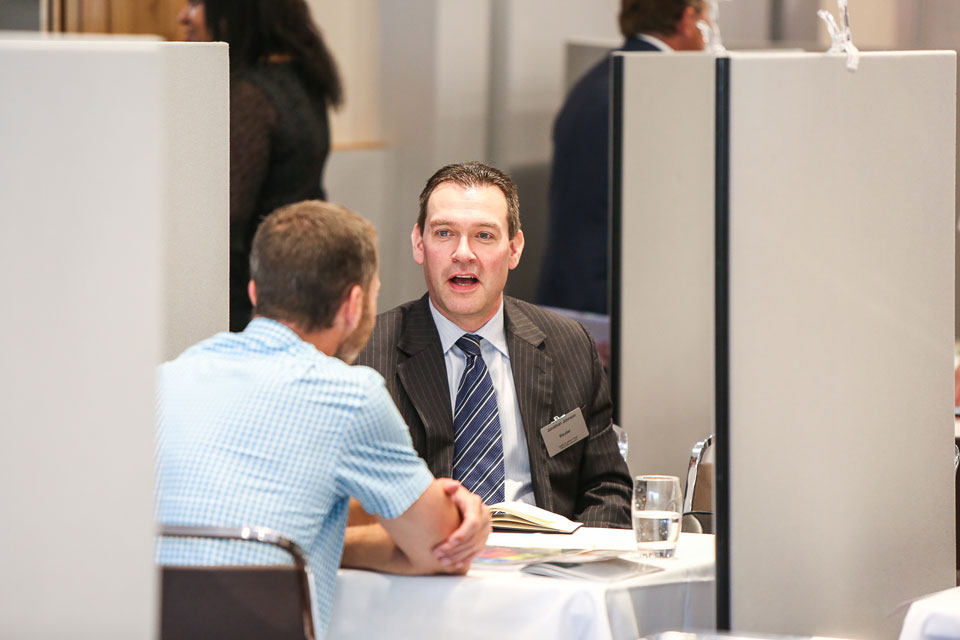
There’s a free guest pass reserved for you to attend the Total Supply Chain Summit in May – make sure you claim it before it’s too late! 18 & 19 May – Heythrop Park, Oxfordshire This unique event is entirely FREE for you to attend – simply reserve your place here. Source new innovative and budget-saving […]
Transport & logistics staff more likely to be off work sick – Study
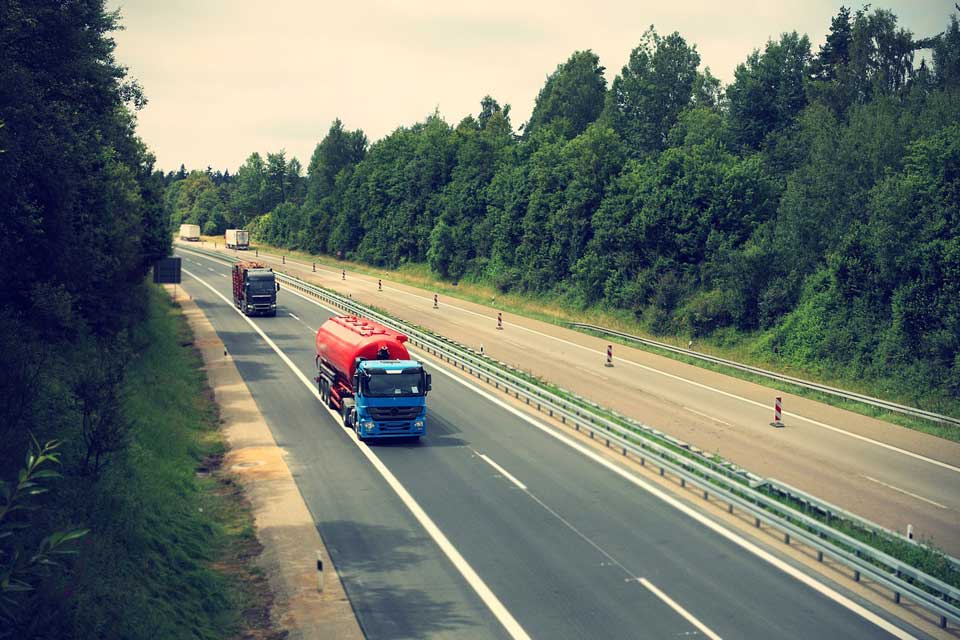
UK transport and logistics workers took nearly three times more sick leave than the average British worker last year, according to new research that identifies the countries most and least notorious for pulling a sickie. The research from time and workforce management solutions provider Mitrefinch, found that transport staff took 11.4 days where other workers in the UK […]
INDUSTRY SPOTLIGHT: QAD DynaSys – Let’s build the future of your supply chain

In 1985, QAD DynaSys was founded in an old bakery by a former planner who saw a need for addressing the planning issues manufacturing companies were facing, thus, developing and launching one of the first computer-based supply chain planning software. QAD DynaSys began by supporting a few large food and beverage customers from their headquarters in Strasbourg, France. […]
Establishing an ethical and sustainable supply chain

Insight from Mark Morley (pictured), Director, Strategic Product Marketing, OpenText What factors are driving businesses to reconsider their supply chain and whether it is set up for ethical sourcing? “Last year, supply chain research specialists APICS found that 83% of supply chain professionals thought ethics were extremely or very important for their organisation. When you consider the […]
Meet the best solution providers at the Fleet Summit
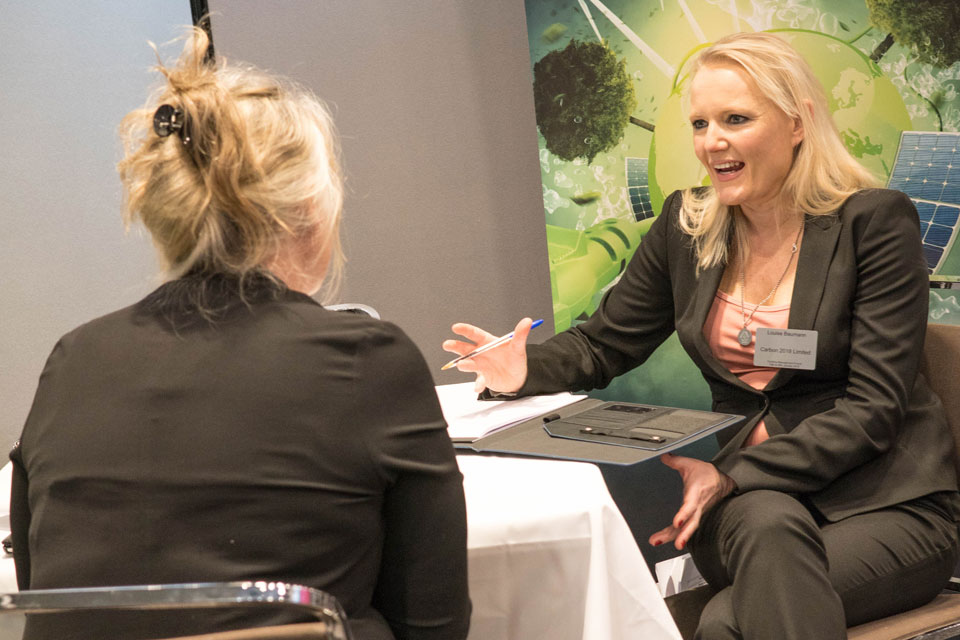
Join us on June 8th & 9th at the Fleet Summit – it will be the best two days you spend out of the office this year. This is a bespoke and highly-targeted two-day event created specifically for senior fleet professionals like you. It is entirely FREE for you to attend. Simply register your place here. When: 8 & 9 June […]
Total Supply Chain Summit – Don’t miss out!
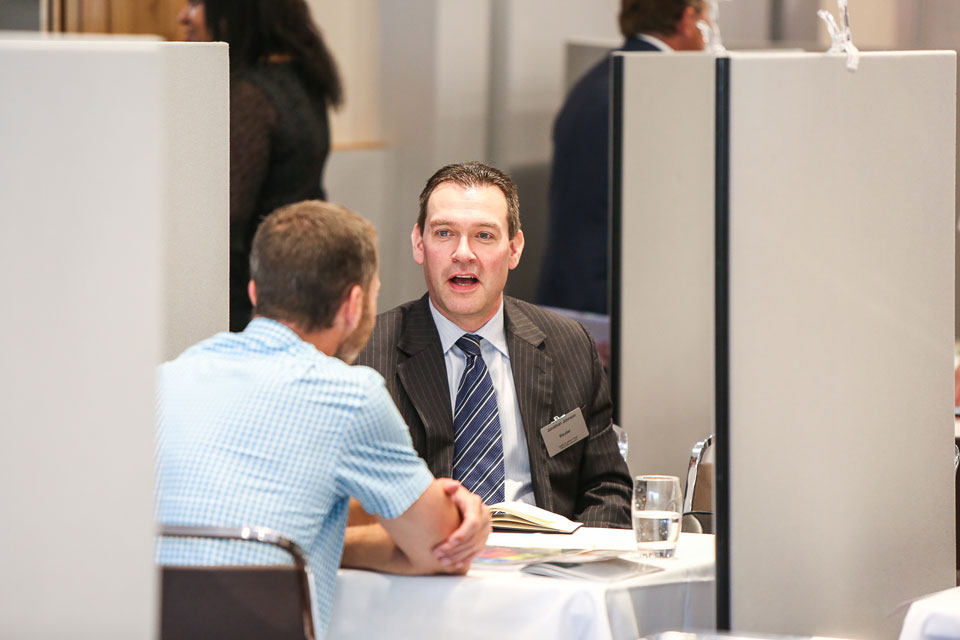
There’s a complimentary guest pass reserved for you to attend the Total Supply Chain Summit. Can you join us? 18 & 19 May – Heythrop Park, Oxfordshire This unique event is entirely FREE for you to attend – simply reserve your place here. Source new innovative and budget-saving suppliers Learn from inspirational seminar sessions hosted by […]
Do you specialise in Delivery Management? We want to hear from you!
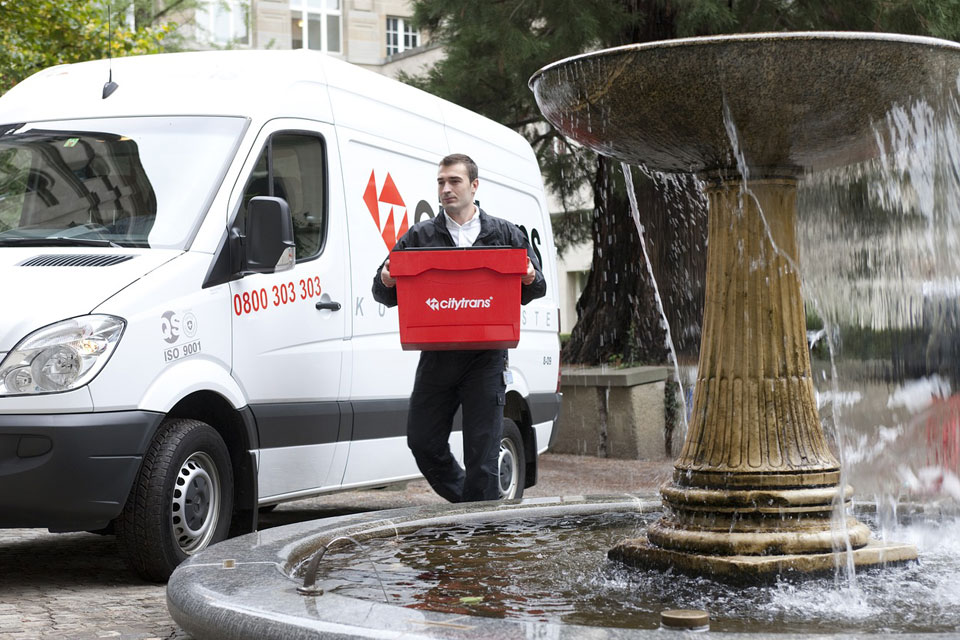
Each month on Supply Chain Briefing we’ll be shining the spotlight on a different part of the logistics and distribution market – and in January we’ll be focussing on Delivery Management. It’s all part of our ‘Recommended’ editorial feature, designed to help supply chain industry buyers find the best products and services available today. So, if you’re […]