The Total Supply Chain Summit is coming to Manchester in October – Can you afford not to be there?
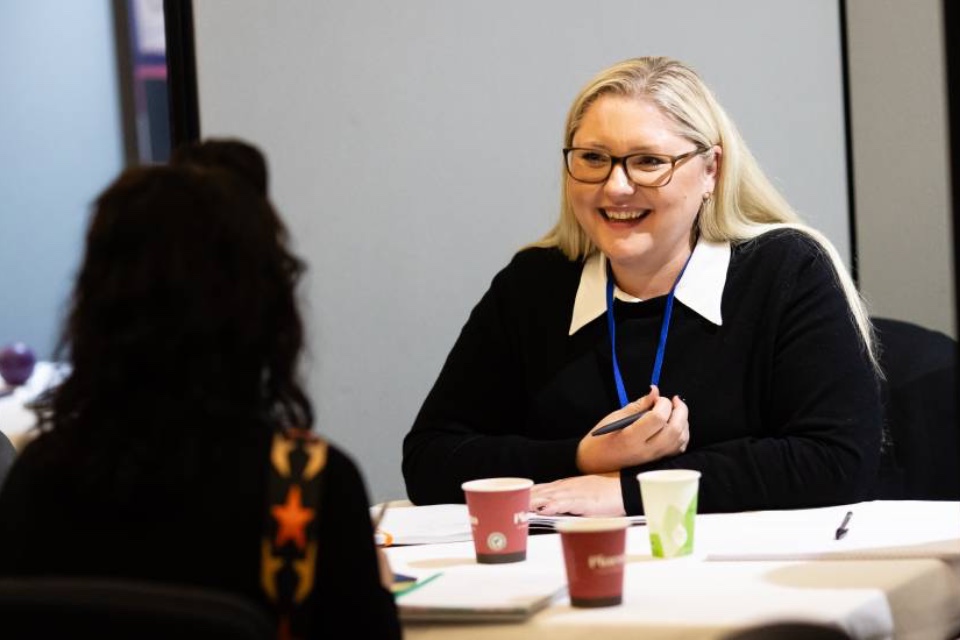
The Total Supply Chain Summit, hosted by Forum Events, offers you two full days of networking, insightful business sessions and invaluable one to one meetings with suppliers hand-picked to support your business needs. But don’t just take our word for it, here’s what Hush had to say of the last event: Monday 13th and Tuesday 14th October […]
COST REDUCTION MONTH: Collaborative Logistics – Pooling resources to reduce costs and emissions
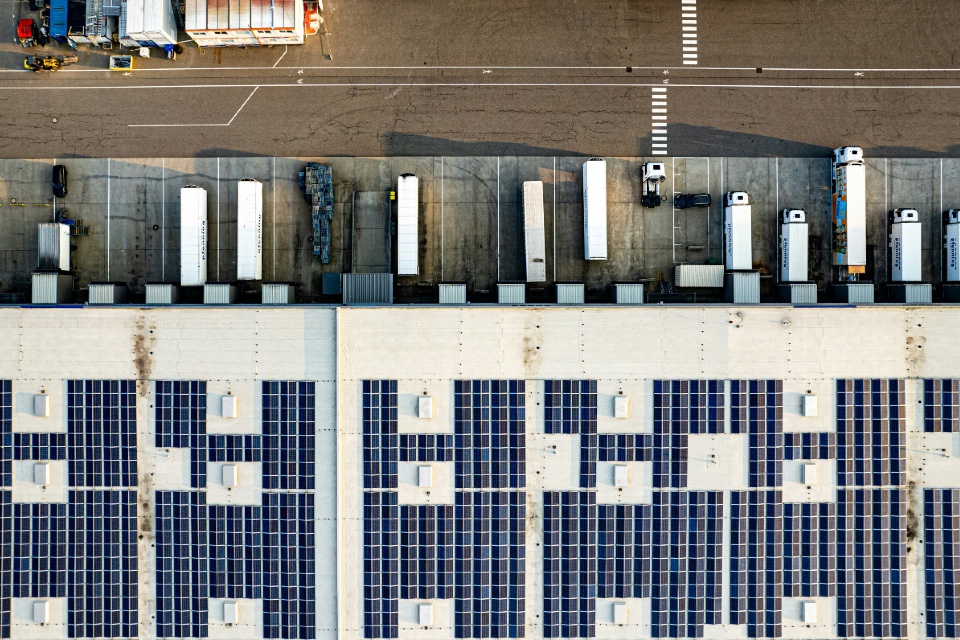
Collaborative logistics is emerging as a powerful strategy for supply chain leaders looking to navigate economic volatility, rising transportation costs, and growing pressure to meet ESG targets. By pooling infrastructure, assets, and operations with industry peers, even competitors, organisations attending the Total Supply Chain Summit are unlocking new efficiencies while cutting carbon emissions. Shared warehousing, […]
July 2025 is Software Solutions Month on Supply Chain Briefing – Here’s how to get involved!
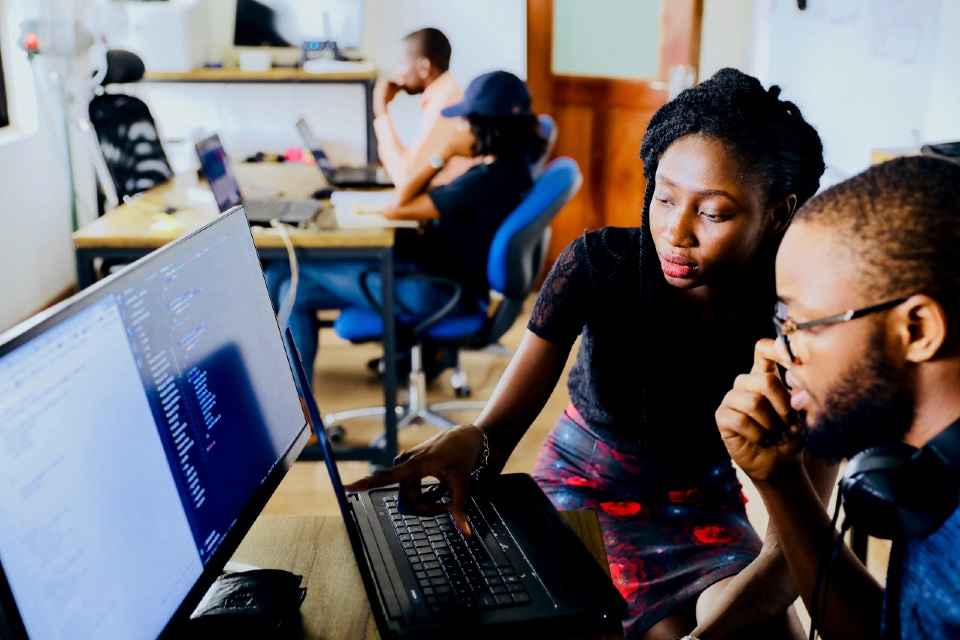
Each month on Supply Chain Briefing we’ll be shining the spotlight on a different part of the logistics market – and in July we’ll be focusing on Software Solutions. It’s all part of our ‘Recommended’ editorial feature, designed to help supply chain industry buyers find the best products and services available today. So, if you’re […]
COST REDUCTION MONTH: How businesses are optimising 3PL and 4PL partnerships for better cost control
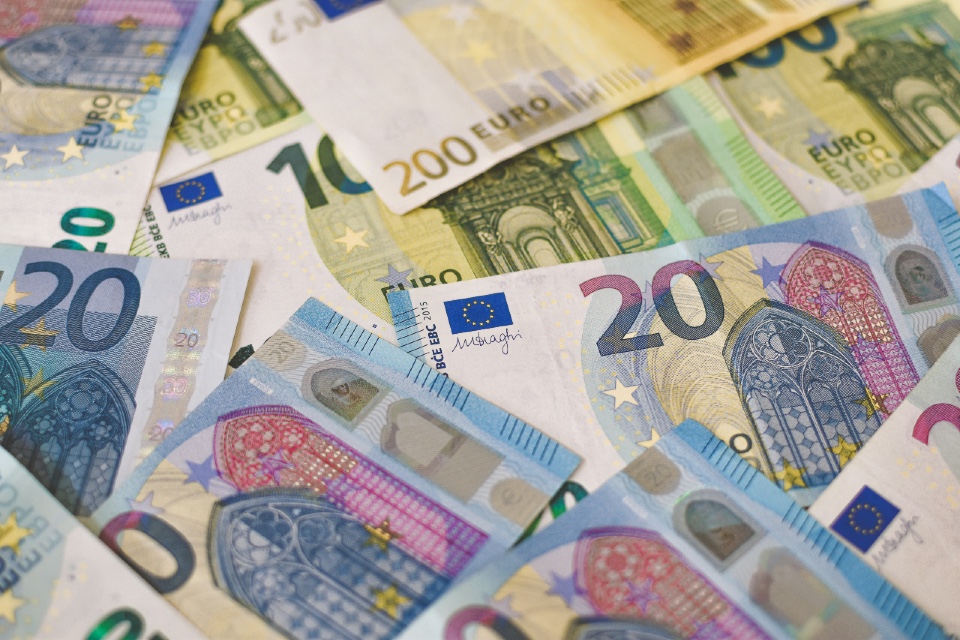
The pressure on supply chain leaders to cut costs without compromising service levels has never been greater. Inflation, fuel prices, labour shortages and global disruptions have prompted many businesses to re-evaluate the effectiveness of their logistics partnerships. As a result, smarter outsourcing strategies, particularly through third-party (3PL) and fourth-party logistics (4PL) providers, are playing a […]
Total Supply Chain Summit: Here’s what your two-day itinerary could look like
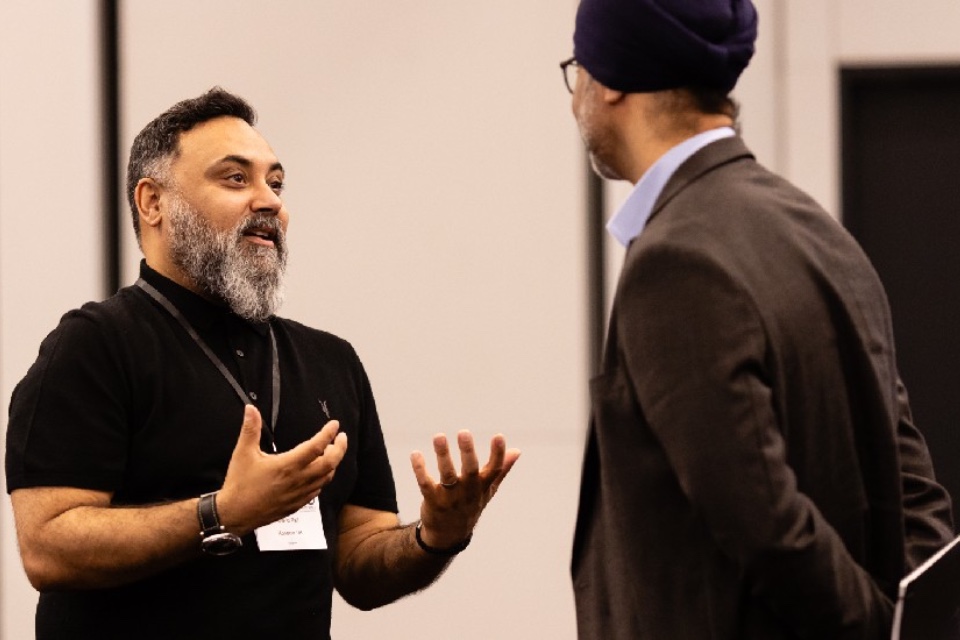
The Total Supply Chain Summit is coming to Manchester in October, offering you two full days of networking, insightful business sessions and invaluable one to one meetings with suppliers hand-picked to support your business needs. Monday 13th and Tuesday 14th October Radisson Blu Hotel Manchester Airport Here’s how your experience will look: Monday 13th October: 08:00-08:45 […]
END-TO-END SOLUTIONS MONTH: 4 steps to finding your organisation’s next partner
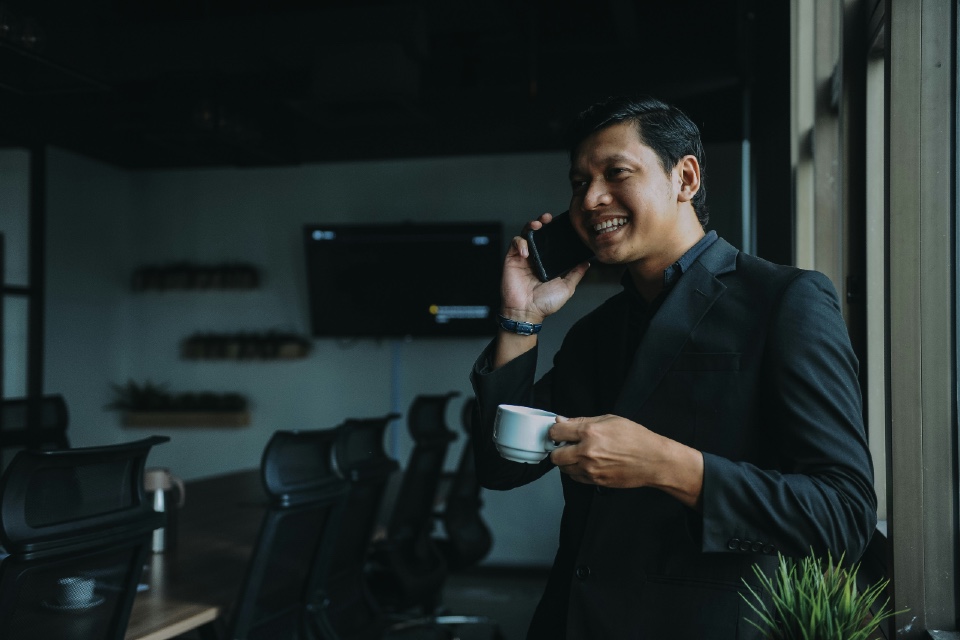
Logistics leaders are under pressure to deliver greater visibility, resilience, and agility across every stage, from sourcing and production to warehousing, transportation, and last-mile delivery. Selecting the right end-to-end supply chain partner is no longer just a tactical decision, it’s a strategic one that can define an organisation’s competitive edge… To maximise value and minimise […]
June 2025 is Cost Reduction Solutions Month on Supply Chain Briefing – Here’s how to get involved!
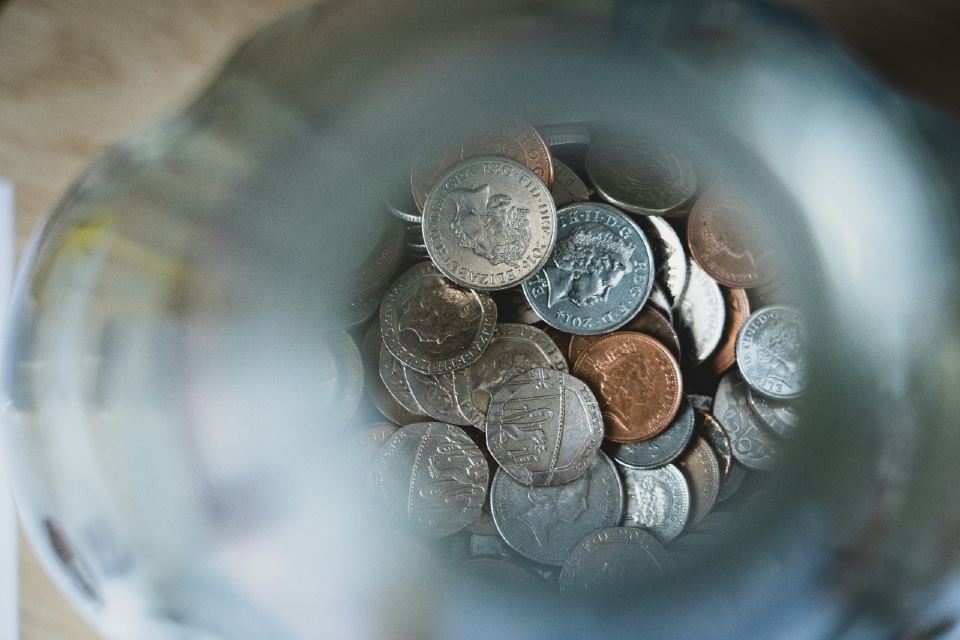
Each month on Supply Chain Briefing we’ll be shining the spotlight on a different part of the logistics market – and in June we’ll be focusing on Cost Reduction Solutions. It’s all part of our ‘Recommended’ editorial feature, designed to help supply chain industry buyers find the best products and services available today. So, if […]
END-TO-END SOLUTIONS MONTH: How integrated supply chain platforms are breaking down silos
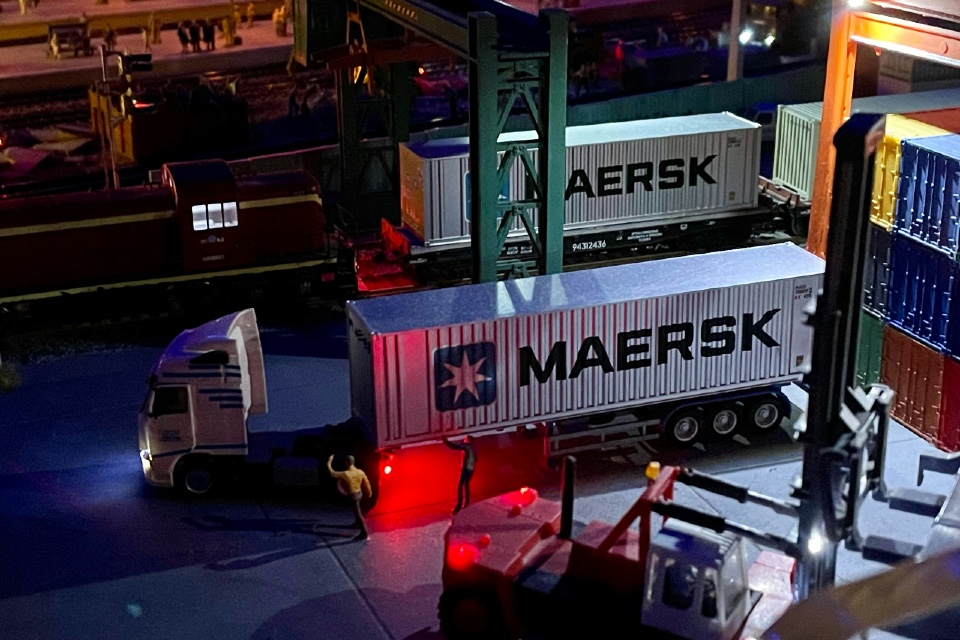
The most competitive supply chains are no longer built on isolated systems or disconnected departments — they are unified, agile, and deeply data-driven. Senior supply chain and logistics professionals across the private and public sectors are embracing a new wave of integrated platforms that bridge the gap between supply chain planning and execution, enabling faster decisions, stronger collaboration, […]
SAVE THE DATE: Total Supply Chain Summit – October 2025
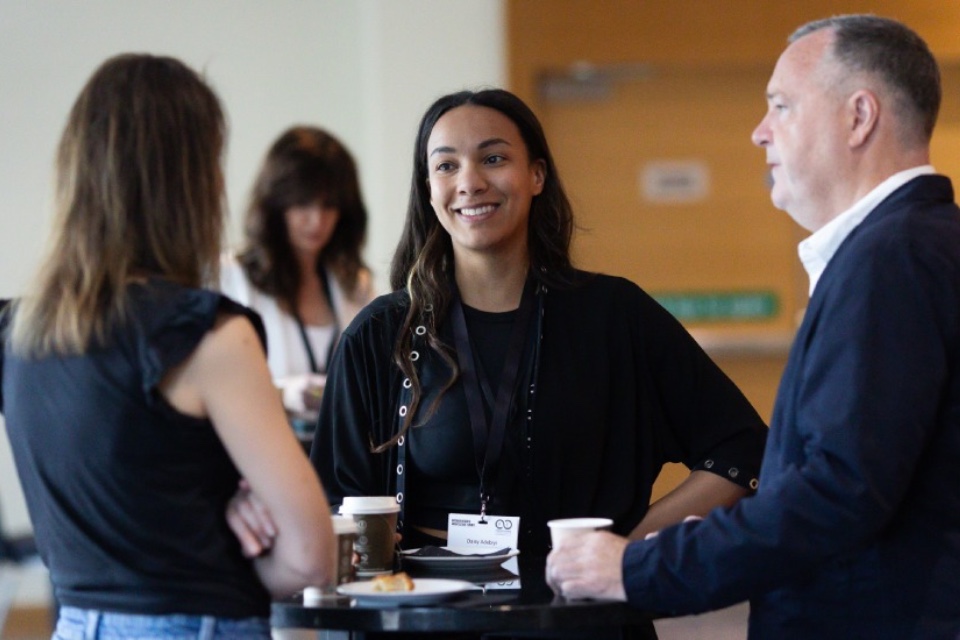
If you couldn’t make last week’s Total Supply Chain Summit, don’t panic! The second of our 2024 events will take place on October 13 & 14th… It’s free for you to attend and could help you reduce your expenditure by matching you up with innovative suppliers who match your business requirements. So register today to secure your […]
WAREHOUSE MANAGEMENT SOFTWARE MONTH: What UK logistics leaders should look for in 2025
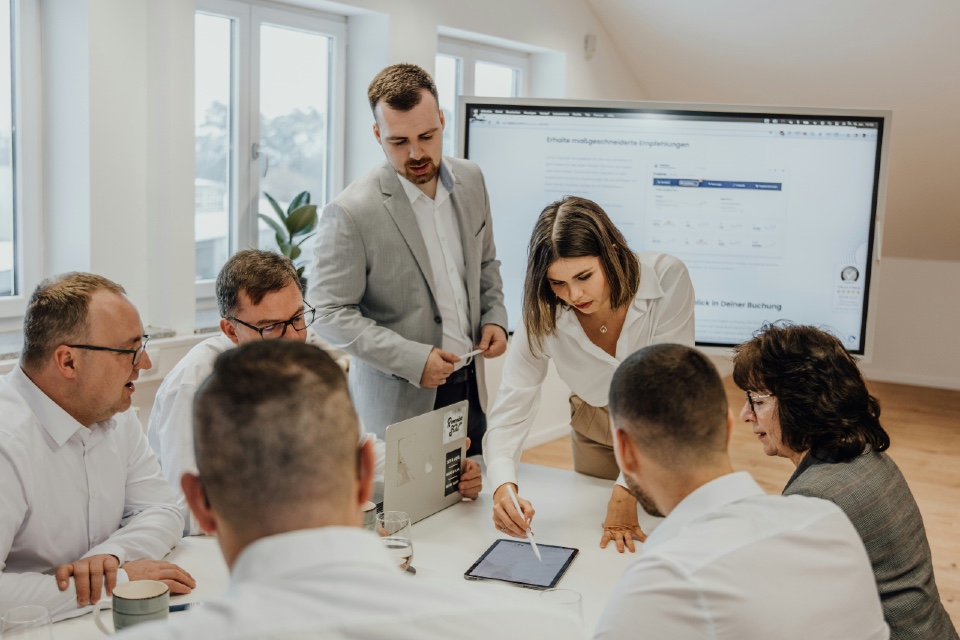
The demands placed on warehouse operations across the UK have never been greater. With rising customer expectations for fast, accurate deliveries, growing pressure to optimise costs, and increased complexity from omnichannel fulfilment, the Warehouse Management System (WMS) has become a critical component of modern logistics infrastructure… However, not all WMS solutions are created equal—and choosing […]