How retailers can stay ahead in the mobile-first era
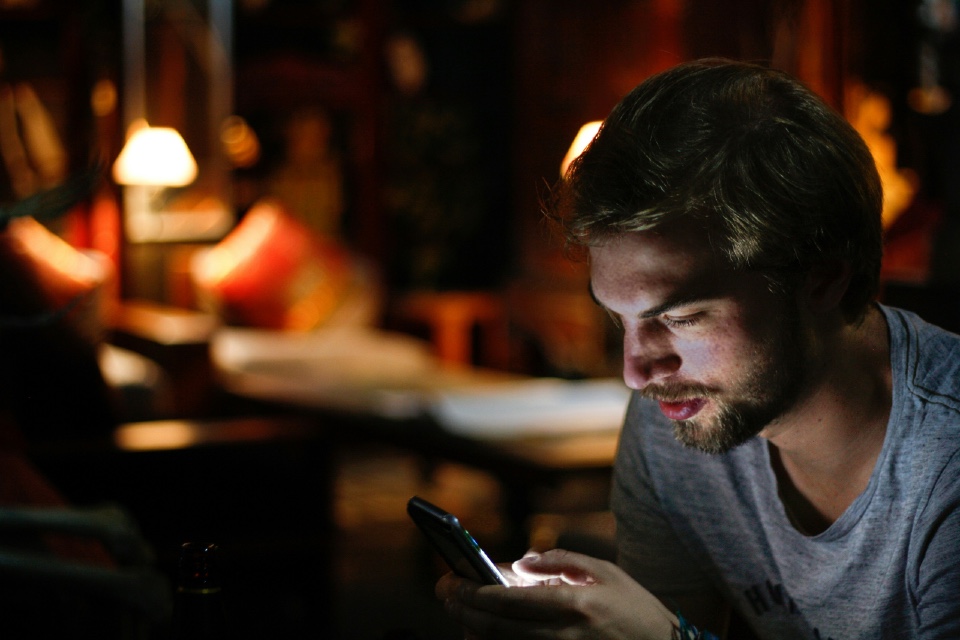
Mobile commerce has had a significant effect on the way people shop, and is now considered an important part of the retail experience. It is expected that revenue from mobile commerce will reach around $2.5 trillion during 2025, nearly doubling over the previous 4 years, and representing a staggering 63% of total retail ecommerce. In the […]
What’s important in a Solution Provider: Beyond Software Quality
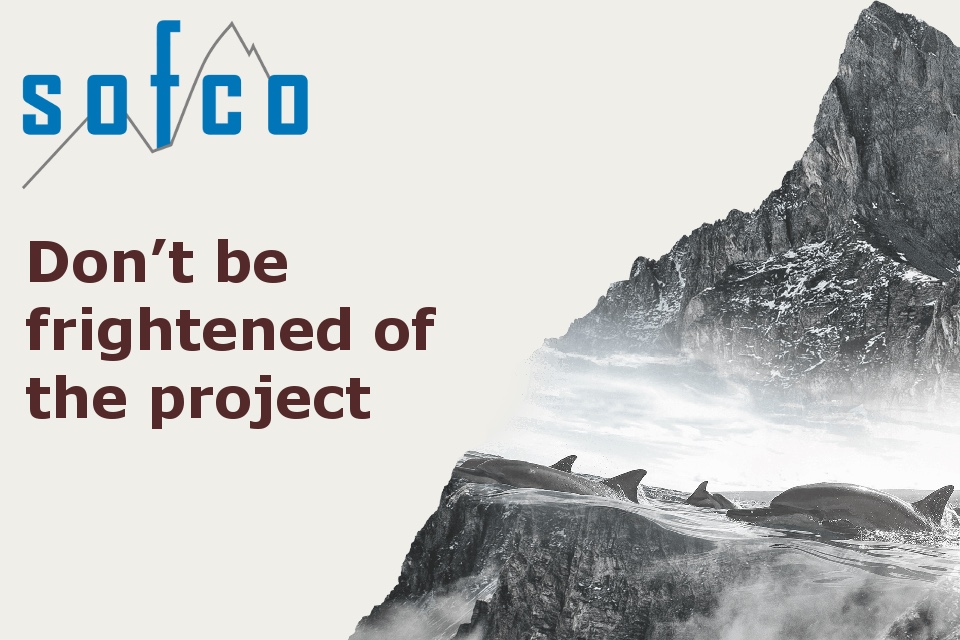
If you’ve worked in industry as long as we have, you will have heard of, or maybe even be battle scarred from, the horror stories of lengthy implementations and the disruption to daily business life and, worse, failed implementations where none of the benefits are realised. At sofco, we really take this to heart as a problem […]
Supply chain visibility – Three reasons behind missing ROI from tech investments
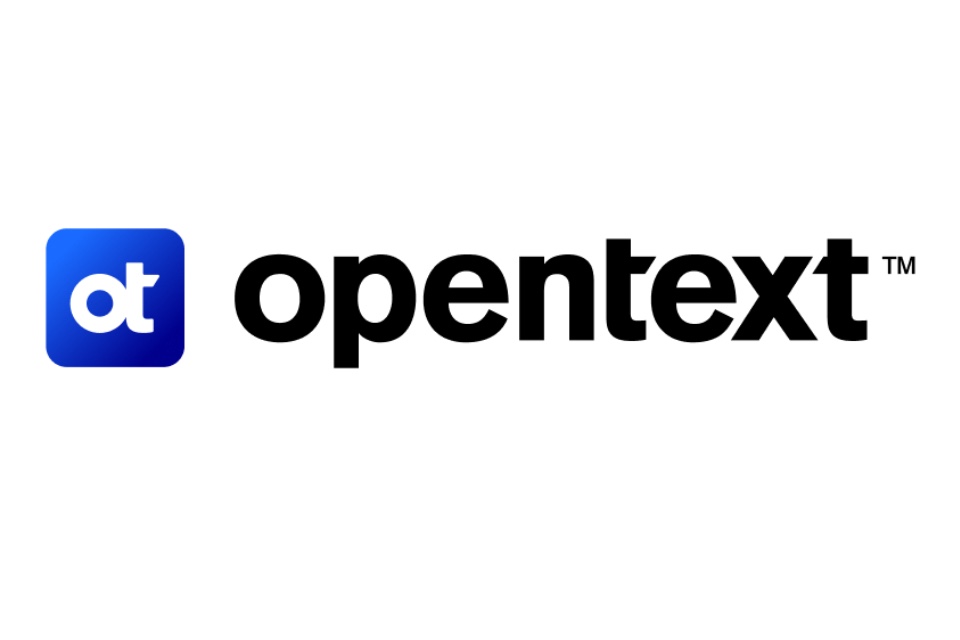
By Open Text Supply chain visibility is a key focus area for many organizations. Therefore, it’s no wonder that visibility, monitoring and analytics tools top the list of supply chain technology investments. Despite the fact that companies both understand the importance of visibility and are investing in tools to improve it, the results are not […]
Are these the top trends in supply chain tech for 2024?
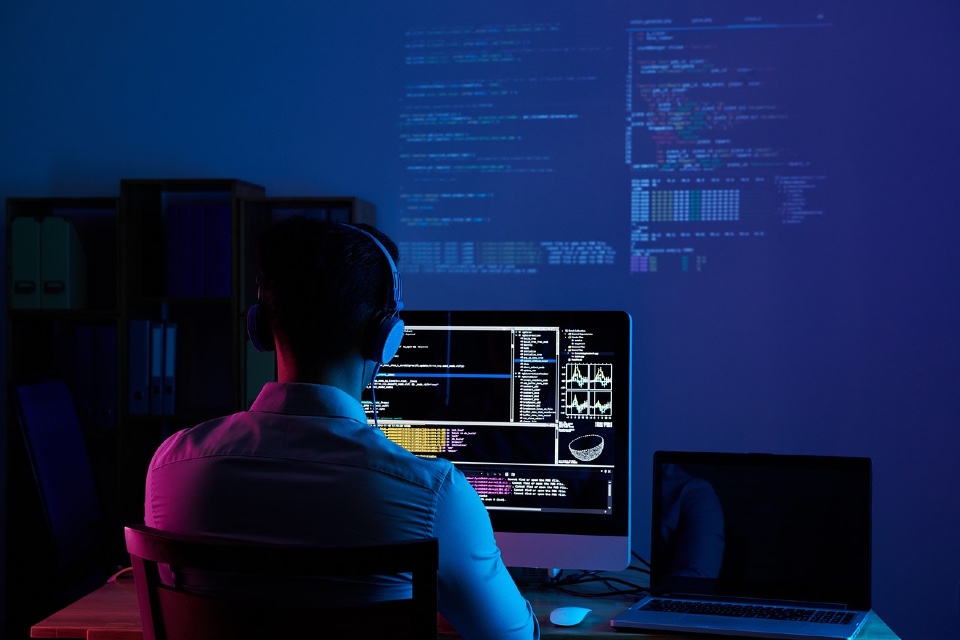
Advancements in technology will provide supply chain technology leaders and chief supply chain officers (CSCOs) with opportunities to support new business models, augment and automate decision making and foster ecosystem collaboration, according to Gartner. With these emerging opportunities, the market analyst has identified the top eight strategic supply chain technology trends for 2024 that will […]
Navigating the Future: Emerging trends in supply chain and logistics
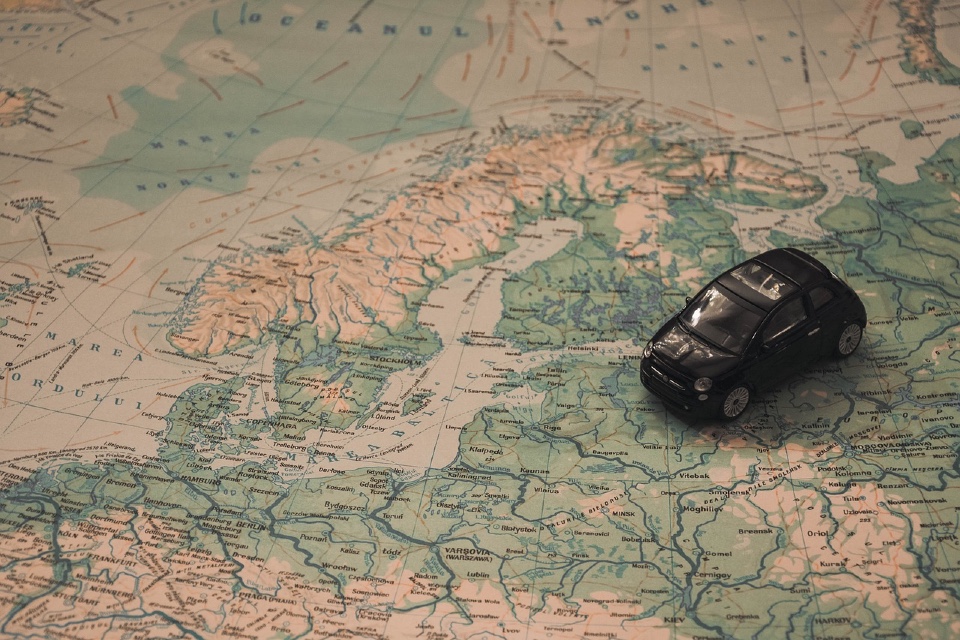
As the backbone of global commerce, supply chain and logistics sectors are in a constant state of flux, shaped by technological advancements, economic shifts, and consumer behaviours. As we move further into the digital age, several key trends are emerging that promise to redefine these critical industries. Firstly, the rise of Artificial Intelligence (AI) and […]
Supply chain productivity declines ‘cannot be solved by technology alone’
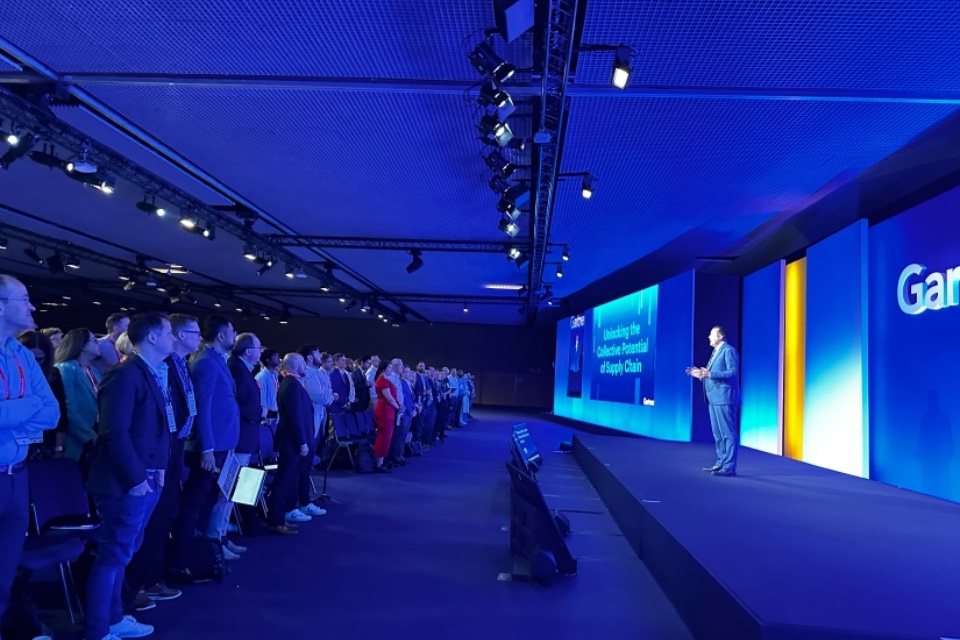
New technologies ranging from smart robotics to actionable AI have the potential to transform the supply chain function, but they will fail to lift historically low levels of labor productivity unless utilised as part of a broader strategy. Gartner experts shared those findings during the opening keynote presentation at the Gartner Supply Chain Symposium/Xpo EMEA, […]
OPINION: Once the supply chain crisis subsides, we can digitally transform our way to a better future

By Quy Le, Head of Delivery, FPT UK It was impossible to go through 2021 without hearing about the crisis afflicting global supply chains. Back in the first quarter of 2020 the pandemic triggered a catastrophic sequence of events that would ultimately impact how efficiently the world’s distribution networks operated. As Covid-19 ripped across the […]
The rise of the virtual supply chain
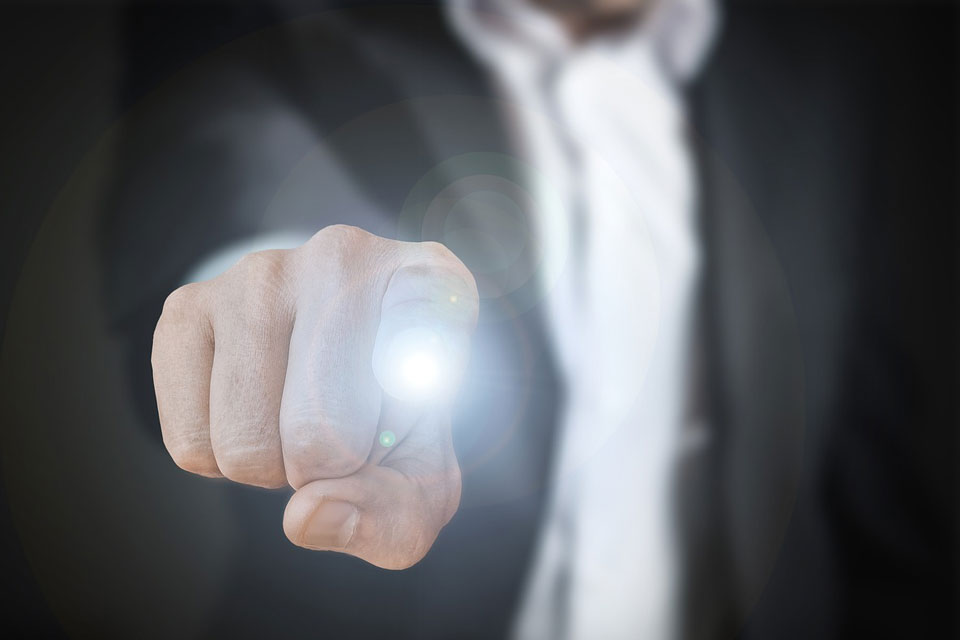
By Adam Bimson, Chief Customer Officer, Vuealta How do you deal with a business that will sell your products, use data and algorithms to adjust product costs, and get said products to your customers in a manner that’s faster, more efficient and far superior to anything you could do yourself? This is a question that publishers […]
Why digitising supply chains can help pay for itself
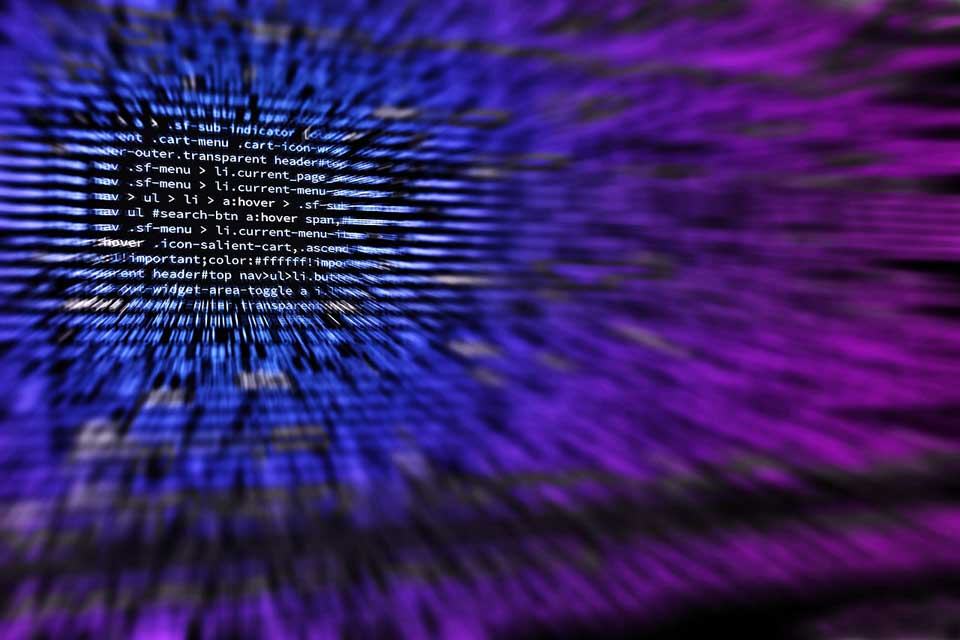
By Derek Bryan, VP EMEA, Verizon Connect For some businesses, digital transformation represents an opportunity to improve how it operates and connects with partners and customers; for others, it can seem like a headache with a considerable price tag attached. While it’s true that any change requires careful planning, those in the ‘loathe camp’ may […]
Fighting plastic pollution with technology
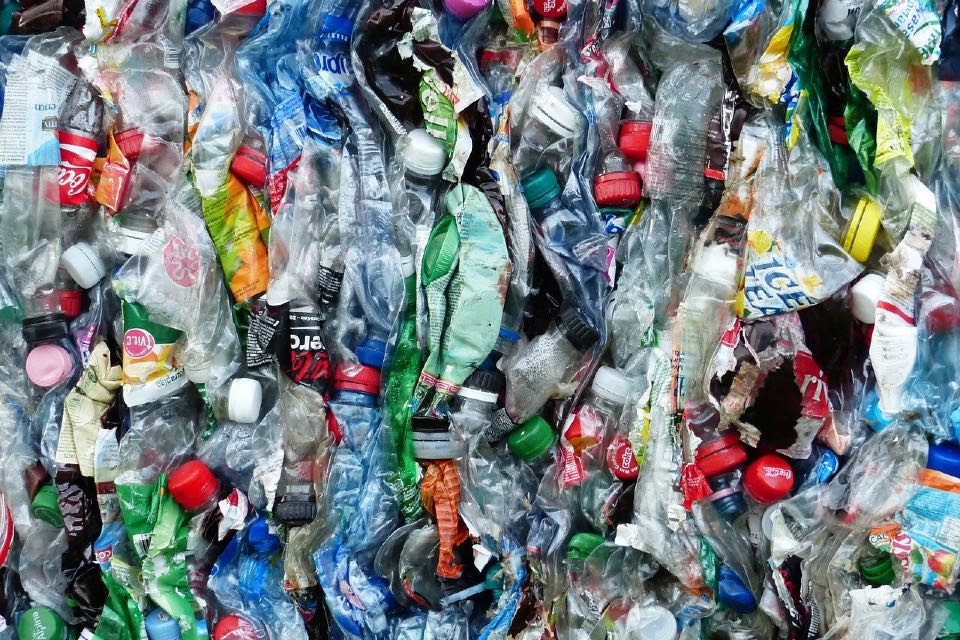
Returnable and re-useable transit packaging and equipment is a key business and environmental asset; unfortunately, a huge amount is lost or stolen each year. Warren Harris, Insight and BD Manager at Bakers Basco tells us how they’re using to tech to cut down on attrition and catch thieves in the act… A major part of the issue […]