Inadequate tech means 95% of companies will fail to enable end-to-end supply chain resiliency by 2026

Most companies will remain locked into an outdated model that will prevent them from achieving end-to-end (E2E) resiliency in their supply chains by 2026. Analysis by Gartner indicates that few companies have accepted the necessary paradigm shift from being forecast-driven, and primarily focused on accuracy, to instead focusing on managing uncertainty in their supply chains. […]
Calls for task force to tackle supply chain resilience

Britain’s manufacturers are calling for a cross-industry and Government taskforce to assess the UK’s current and future supplychain resilience and capabilities, as well as establishing an action plan to protect the economy from any future significant disruptive event. The call was made on the back of a report by Make UK and Infor, ‘Operating without Borders […]
How to build resilience into Supply Chain 4.0 strategies
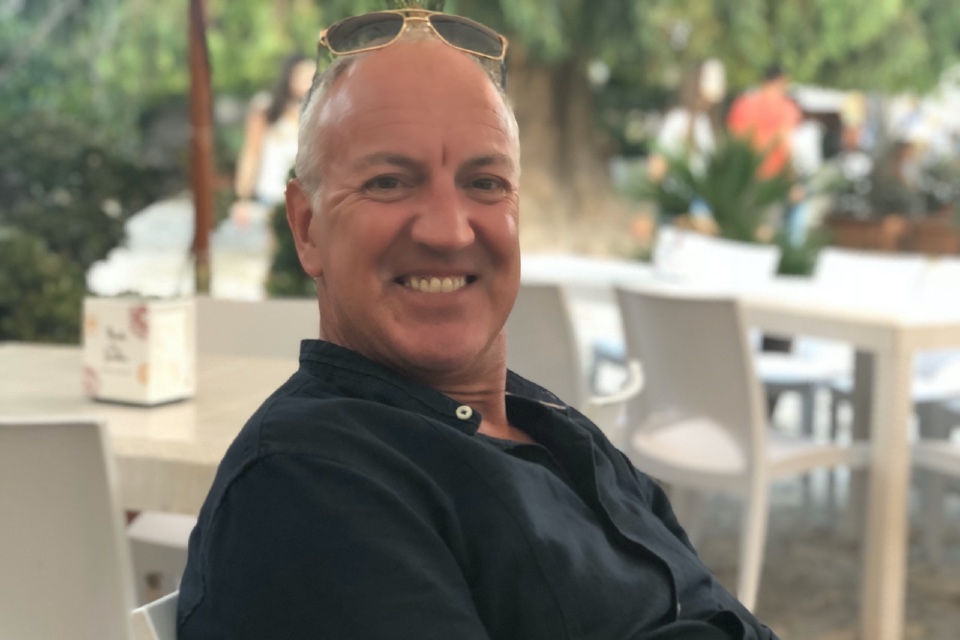
By Ian Terblanche (pictured), Strategic Sales & Channel Director at Sigfox With the rise in supply chain disruptions during COVID-19, companies may already have an eye on streamlining and improving supply chains but they are also under immense pressure to manage supply chain disruption. When examining the challenges faced by supply chains today, companies need […]