Volatile transport costs impacting logistics throughout August
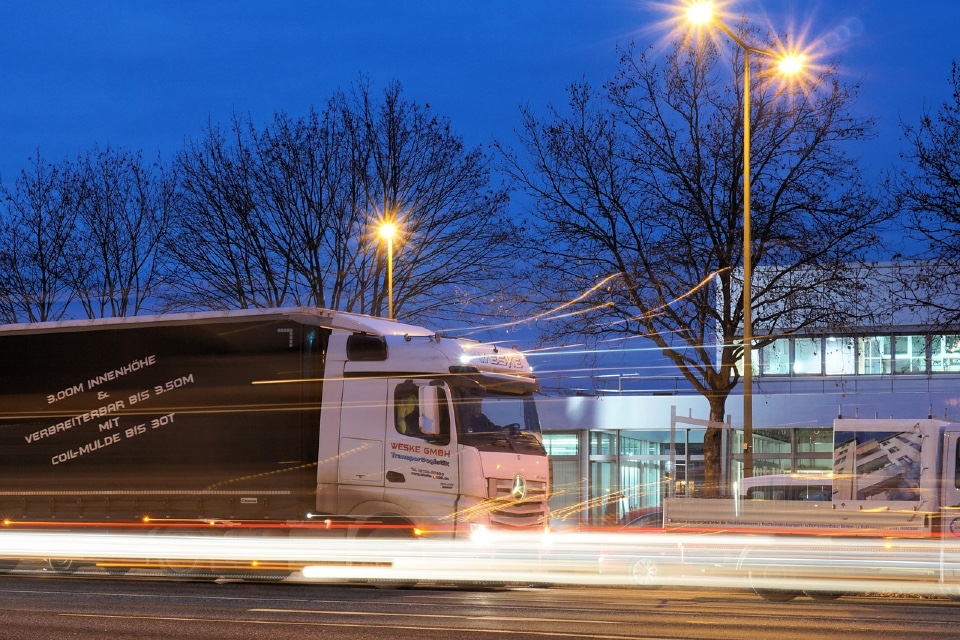
Data from the TEG Road Transport Price Index reveals that road transport prices fell 2.13% during July, with haulage prices dropping just under 4%. However, prices have been relatively stable so far this year, marching slowly upwards since February. The combined haulage and courier index had risen by less than 8 points up to July. […]
Why your supply chain needs a dynamic cost model

By Zencargo The last 18 months have seen the freight market at its most turbulent — and expensive — in living memory. While most shippers know that they’re paying more, monitoring exactly how much more and how it affects profitability remains a challenge. However, by moving to a dynamic cost model, logistics managers can adapt […]
LOGISTICS COSTS GUIDE: Plan easier with logistics simulation

By UniCarriers Logistics Costs The types of cost attached to a goods flow or to internal goods handling may vary from company to company and may also be expressed in many ways. The various types of cost are expressed and collected as a single logistics cost, consisting of: Buildings; Storage equipment; Materials handling equipment (MHE); […]
Environmental supply chain risks to cost companies $120 billion by 2026
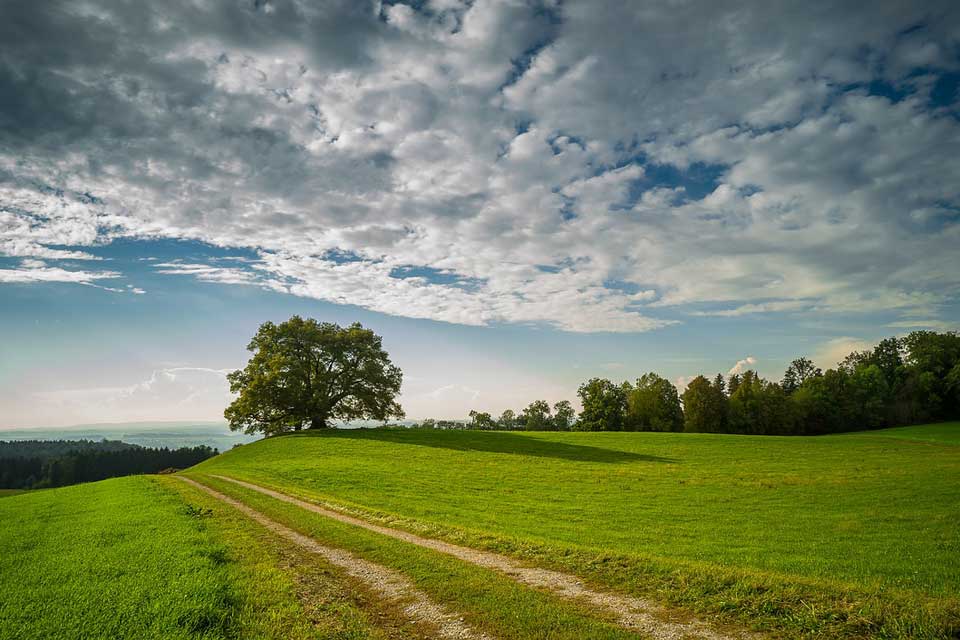
Companies face up to $120 billion in costs from environmental risks in their supply chains by 2026, according to new research released today by CDP. The report, Transparency to Transformation: A Chain Reaction, analyses data from 8,000+ supplier companies disclosing to their corporate customers via CDP in 2020 and finds a combined $120 billion of increased costs among those companies […]
Redistributing surplus food to charities ‘saves the UK economy £51m every year’
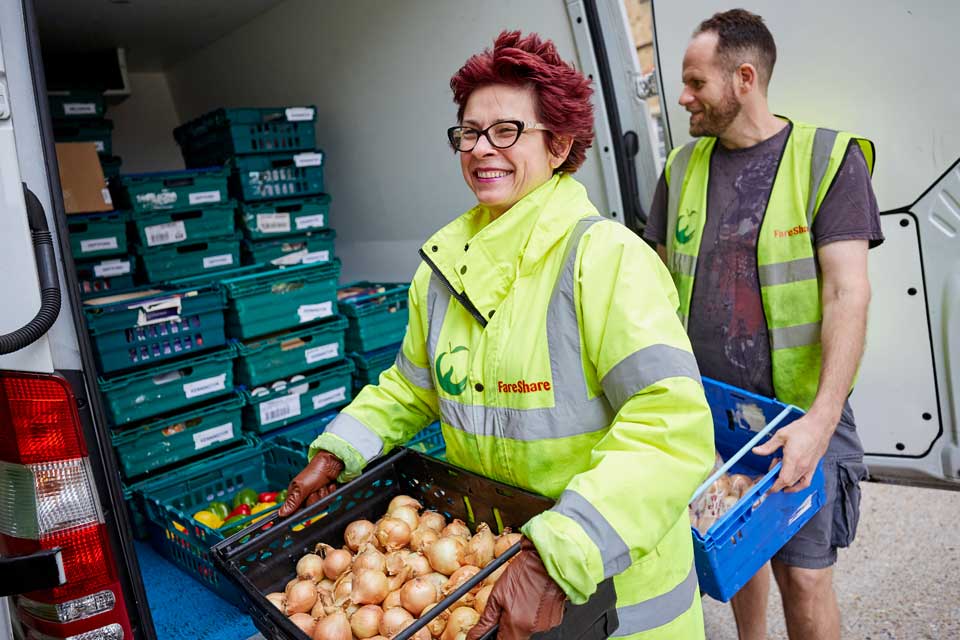
A new impact report released by FareShare claims that collecting food that would otherwise go to waste and redistributing it to good causes saves the UK economy approximately £51 million every year. The Wasted Opportunity Report, carried out by NEF consulting, evaluates the economic and social value of redistributed surplus food, as well as the […]