Hospitality supply chain ‘on verge of collapse’
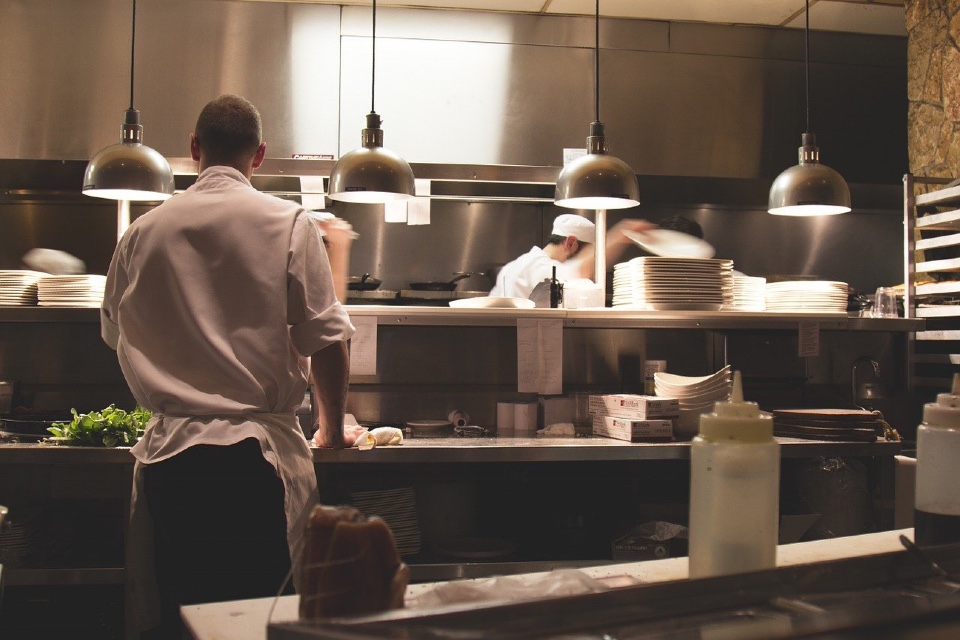
The UK’s hospitality sector supply chain is facing devastation with 324,000 jobs at risk unless businesses receive immediate financial support from the Government, according to new research. UKHospitality’s Supplier Alliance has released data highlighting the impact of the COVID crisis on the hospitality supply chain and the lack of financial support that has been received […]
Retailers to on-shore £4bn of products to the UK as COVID-19 ‘resets’ supply chain strategies
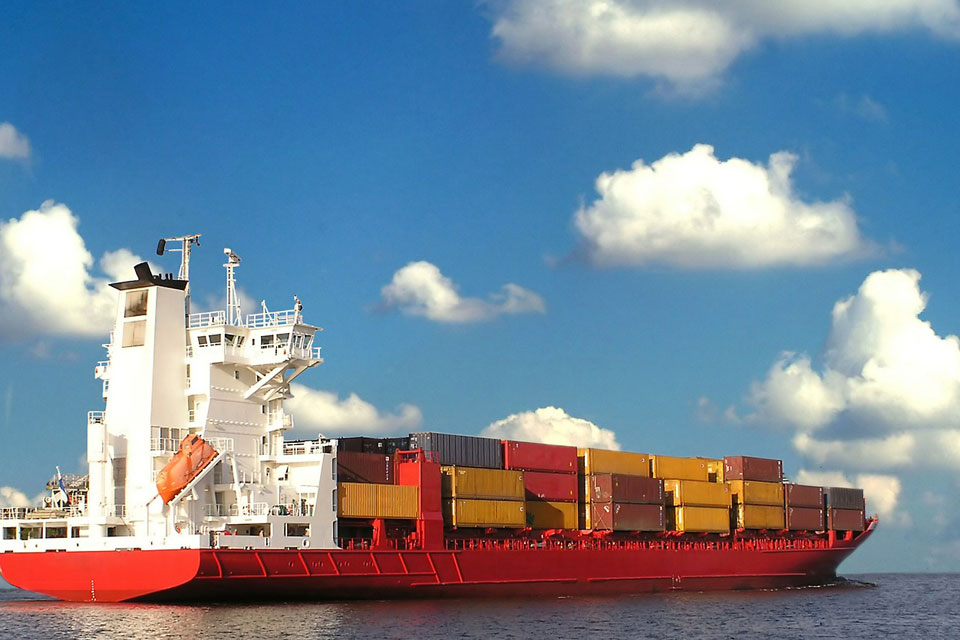
More than £4.2 billion of products will be on-shored to the UK by retailers in the next 12 months in a move that would represent a significant fillip to manufacturing, being equivalent to the country’s entire current clothing manufacturing output. That’s according to a new report by global professional services firm Alvarez & Marsal, in partnership […]
Navigating Covid-19 through e-commerce: Lessons learnt
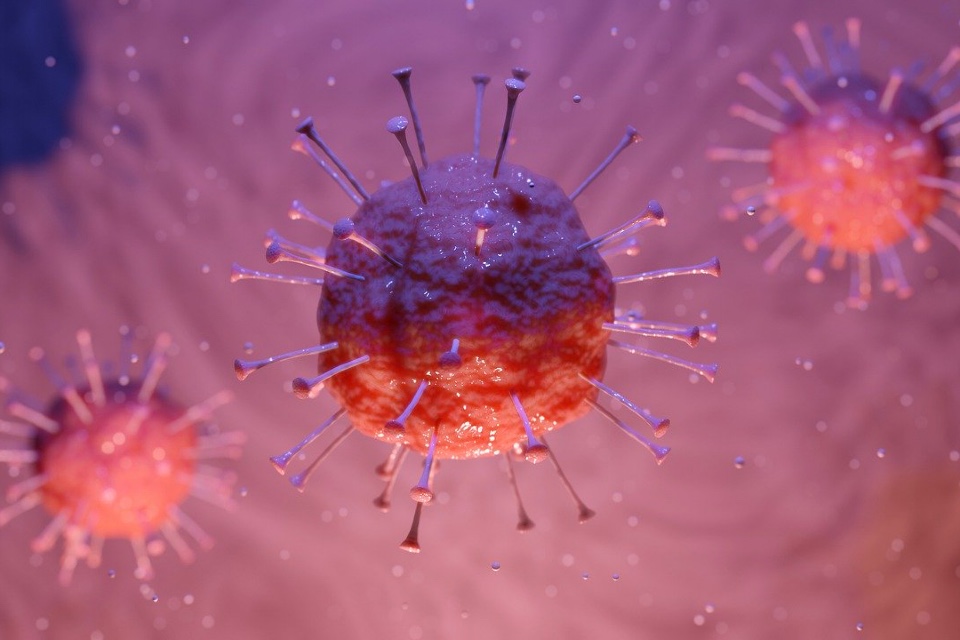
By Michiel Schipperus, CEO at Sana Commerce Covid-19 has had a significant impact on the global retail industry, with sales expected to dip by 5.7% this year. At the same time however, global Amazon sales increased by 26% in Q1 and 40% in Q2, and e-commerce spending in the U.S. grew from 11.8% in Q1 to 16.1% in Q2. In the […]
Smart warehousing: A reality check for the big vision of the Internet of Things

By Jamies Watts, Head of Sales, Mysoft Following last week’s Total Supply Chain Summit, I have reflected on some of the conversations I had with people and a key topic that came up was Smart Warehousing and where SME’s are on their journey to optimizing towards this. I have done some further reading and wanted to […]
OPINION: UK Business ill-prepared for post-Brexit Customs Complexity
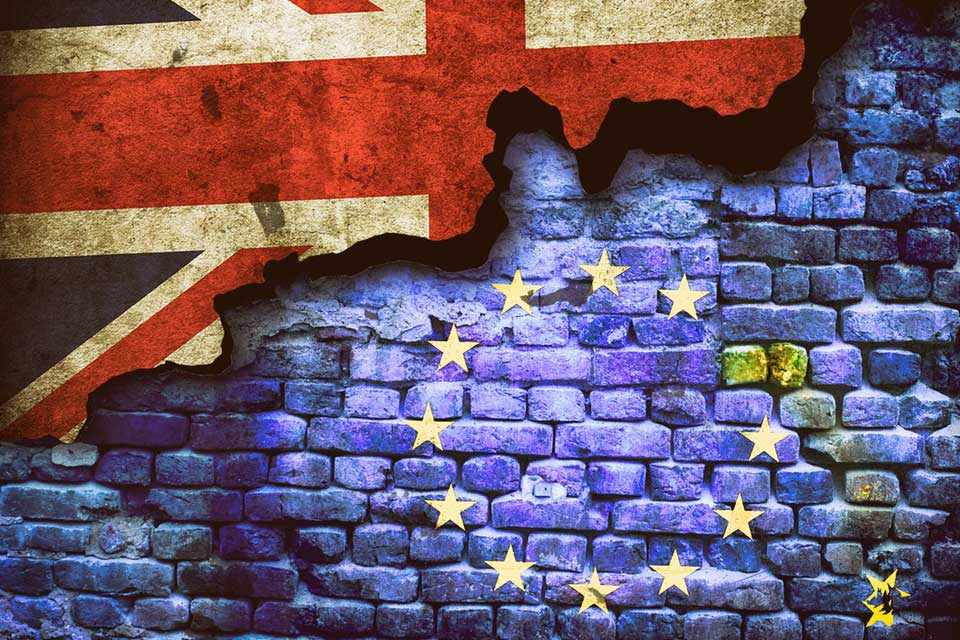
2020 was meant to be the year of ‘Brexit Preparation’. When the UK left the EU on January 1st2020, firms involved in trade with the EU were set to spend 12 months on robust planning, maximising the 12 month Brexit transition period to understand the new trade and customs requirements. The transition period provided time […]
5 Minutes With… Matthew Hopkins, BoxLogic

In the latest instalment of our supply chain industry executive interview series we spoke to Matthew Hopkins, Director at BoxLogic, about his company, industry opportunities, the challenges posed by COVID-19 and Brexit, plus some Netflix favourites… Tell us about your company, products and services. BoxLogic is a consultancy that supports our clients transform their supply […]
How COVID-19 has impacted global supply chains
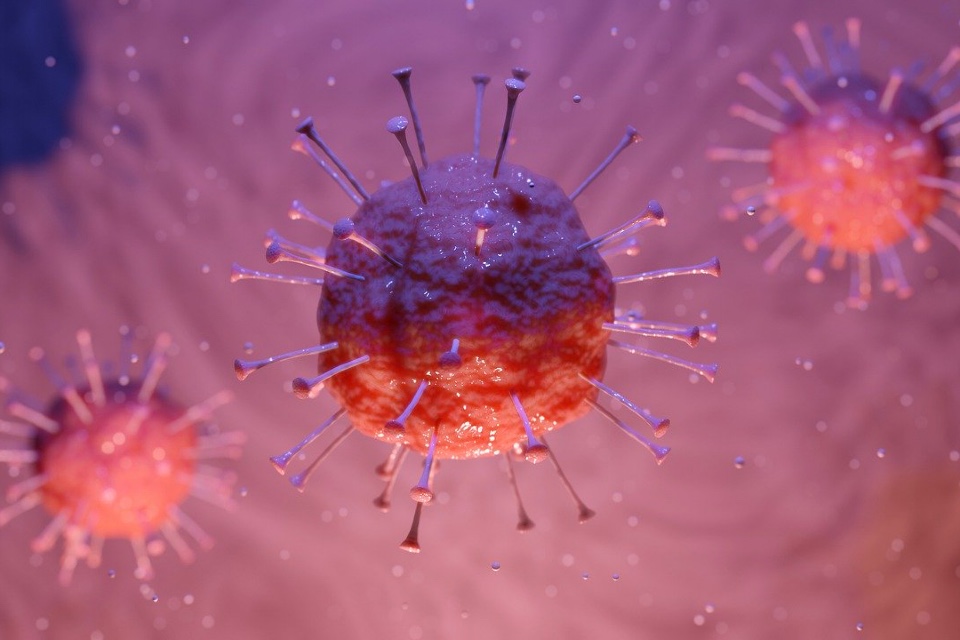
By Nick Pike, Chief Revenue Officer, Vizibl The impact of COVID-19 has been swift and devastating to those directly affected. Not just from a health perspective, but also for businesses who had to promptly close their doors as the country went into lockdown, particularly those in hospitality and retail. And as we now slowly emerge […]
The value of global trade insights in navigating COVID-19 supply chain disruptions
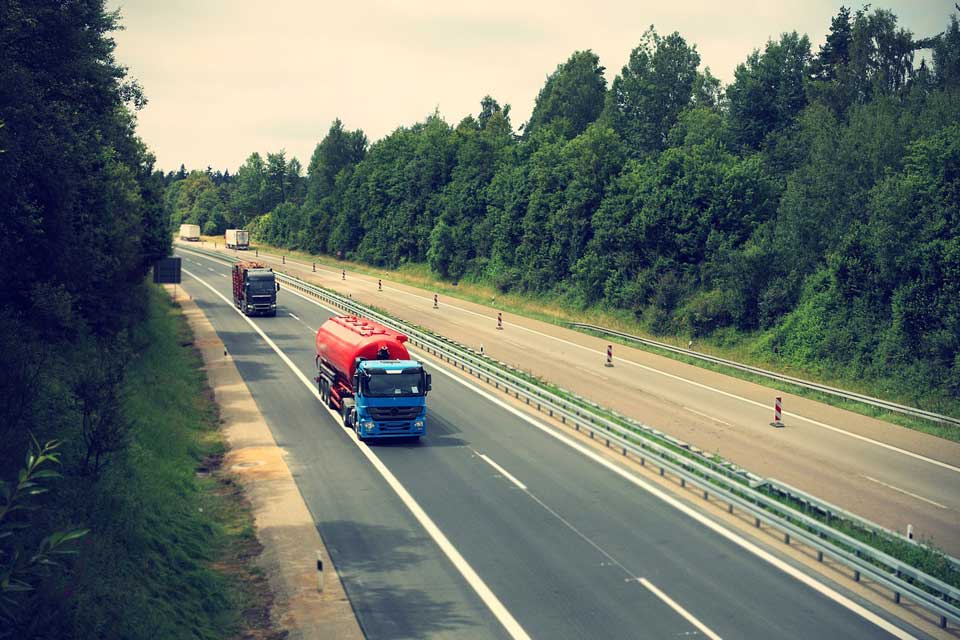
By Mark Segner, VP Global Sales, Descartes The Coronavirus pandemic has exposed the fragility of the modern supply chain, as companies struggle to acquire the products and raw materials needed to keep revenue flowing. With many businesses relying heavily on a limited number of trading partners, many located in hard-hit areas like China, the scale of […]
Survival, resilience and growth: A report on the UK’s economic recovery

As lockdown restrictions around the UK are easing, businesses are taking steps on the road to recovery. The coronavirus (COVID-19) pandemic has impacted companies of all sectors and sizes, so the chance to revive operations and look to the future is a welcome shift for millions of small and medium-sized enterprises (SMEs). While many businesses haven’t been […]
Making tomorrow a better world in logistics

By Michel Waterschoot, Sales Manager – Southern Europe, Northern Africa, Middle East, Descartes The health crisis that we are currently experiencing, as well as its financial and economic consequences, should not mean we lose sight of the opportunities that can be leveraged today to help businesses continue growing and developing. This situation should be used […]